(Ed Note: In a previous article, we took you through the ins and outs of Diamond-Like Carbon (DLC) Flat Tappet Lifters and how they address some issues associated with traditional flat tappets. This article focuses on hydraulic roller lifter technology — more specifically, COMP Cams’ relatively new Evolution Lifters — and why you should consider them for your next build.)
Lifter History
Lifters play a crucial role in the valve train as they convert the camshaft’s rotation into vertical motion to open and close the intake or exhaust valves. In the early days of internal combustion engines, valve trains used a simple cam and follower mechanism without lifters. This design used a flat-faced cam that pushed directly on the valve stem, guided by a simple rocker arm or a tappet.
As engines became more advanced and powerful, the need for more precise valve operation became apparent. This led to the development of solid lifters, which provided a more reliable means of opening and closing the engine’s valves. Solid lifters worked well (and still do), but they must be adjusted periodically to maintain proper valve clearance.
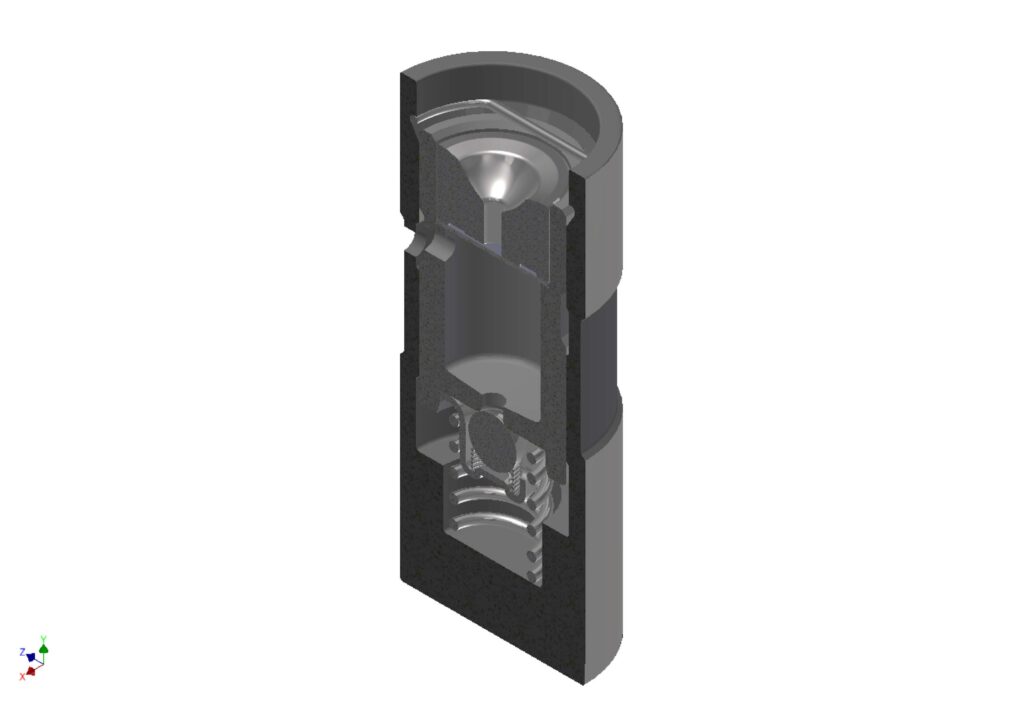
Auto manufacturers began using hydraulic flat tappet lifters in the mid-1940s, allowing for quieter operation and reduced maintenance compared to solid lifters. Initially used in high-performance engines to improve power and durability, they were integrated into most production engines as they became more affordable and reliable. Their widespread adoption didn’t occur until the 1950s and 1960s.
The development of hydraulic lifters was a significant advancement in engine technology until GM introduced hydraulic roller lifters in the mid-1980s on Corvettes and Camaro Z28s. They offered several advantages over solid and traditional hydraulic lifters, including improved high-RPM performance, durability, less noise, and reduced valve train wear. Since costs came down by the 1990s, they have been widely adopted in many production engines.
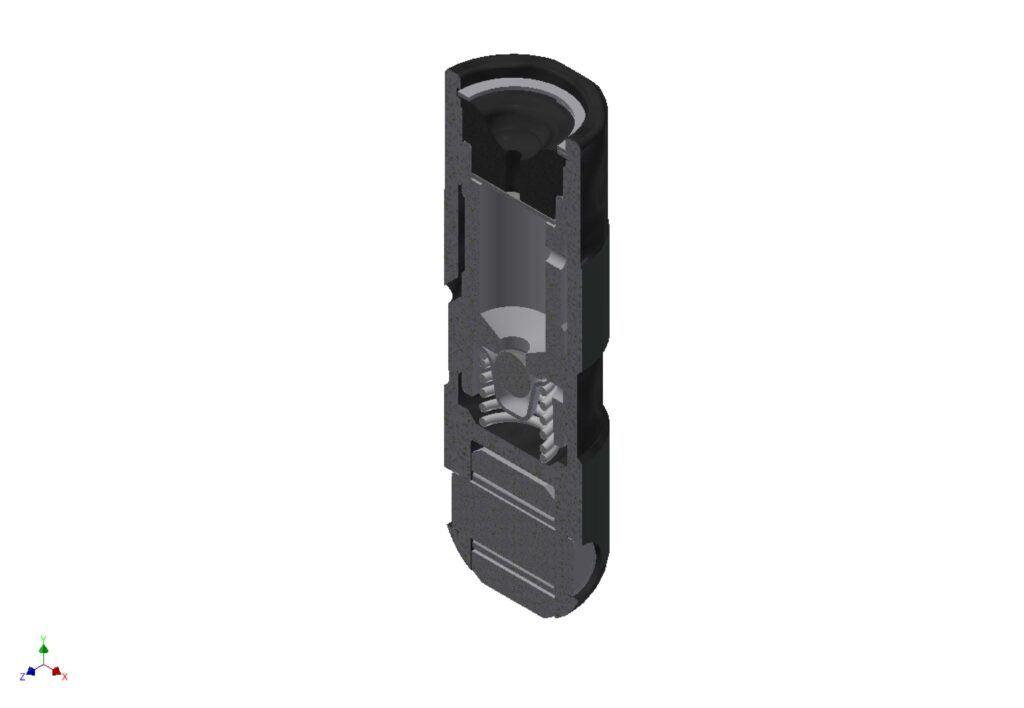
Potential Problems
While hydraulic roller lifters are generally reliable, offering several advantages over solid and traditional hydraulic lifters, there are still a few things to consider when choosing lifters.
1. Oil Issues – Engine oil is critical to the proper function of the lifters, so it needs to be clean and have the appropriate viscosity to function correctly.
2. Blockage – The hydraulic passages can get blocked with debris or sludge, causing the lifter not to work correctly.
3. Bleed-down – If the lifter can’t maintain proper oil pressure, it won’t be able to keep the correct valve lash.
Regular oil changes using quality grade oil is the best way to stave off these issues, but your typical stock lifters will eventually wear out. When you’ve had enough of ticking lifters and inconsistent power, COMP Cams has a premium upgrade offering excellent durability and reliability at an economical price point.
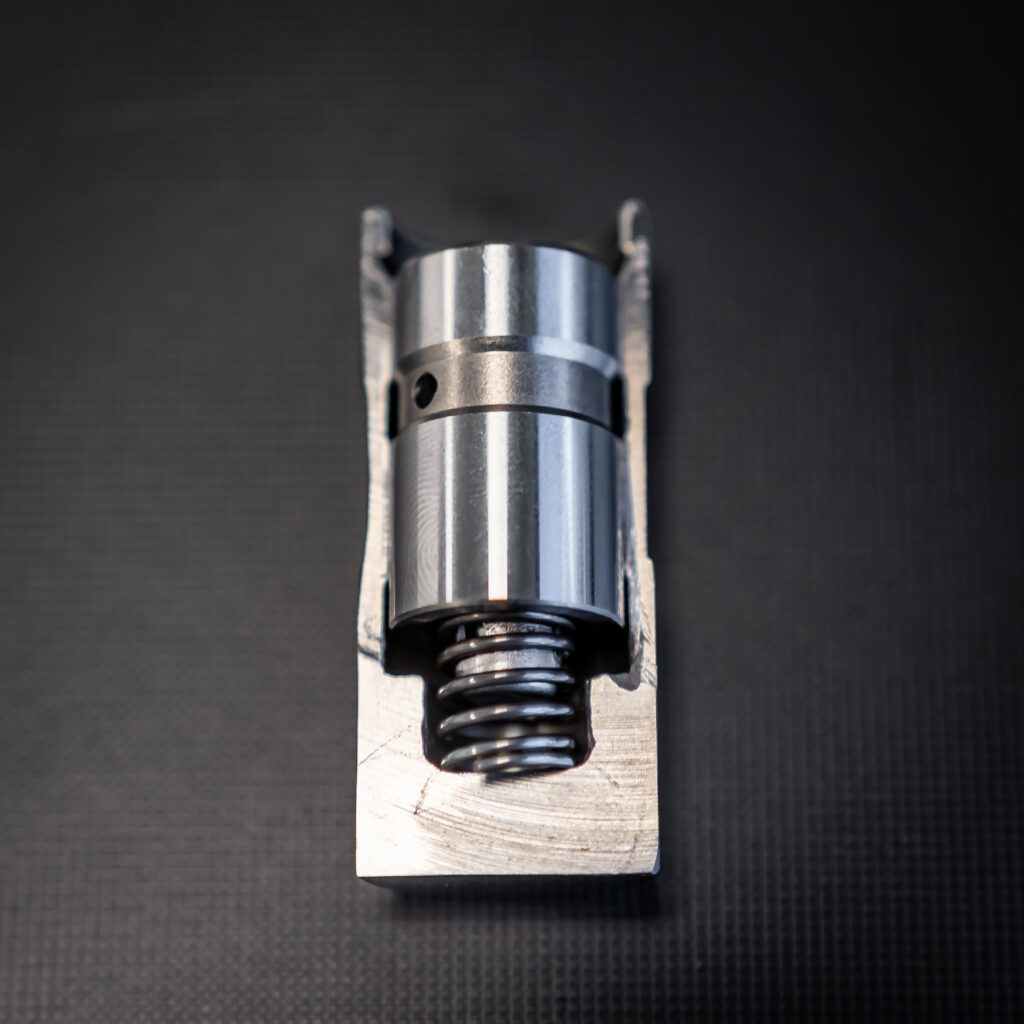
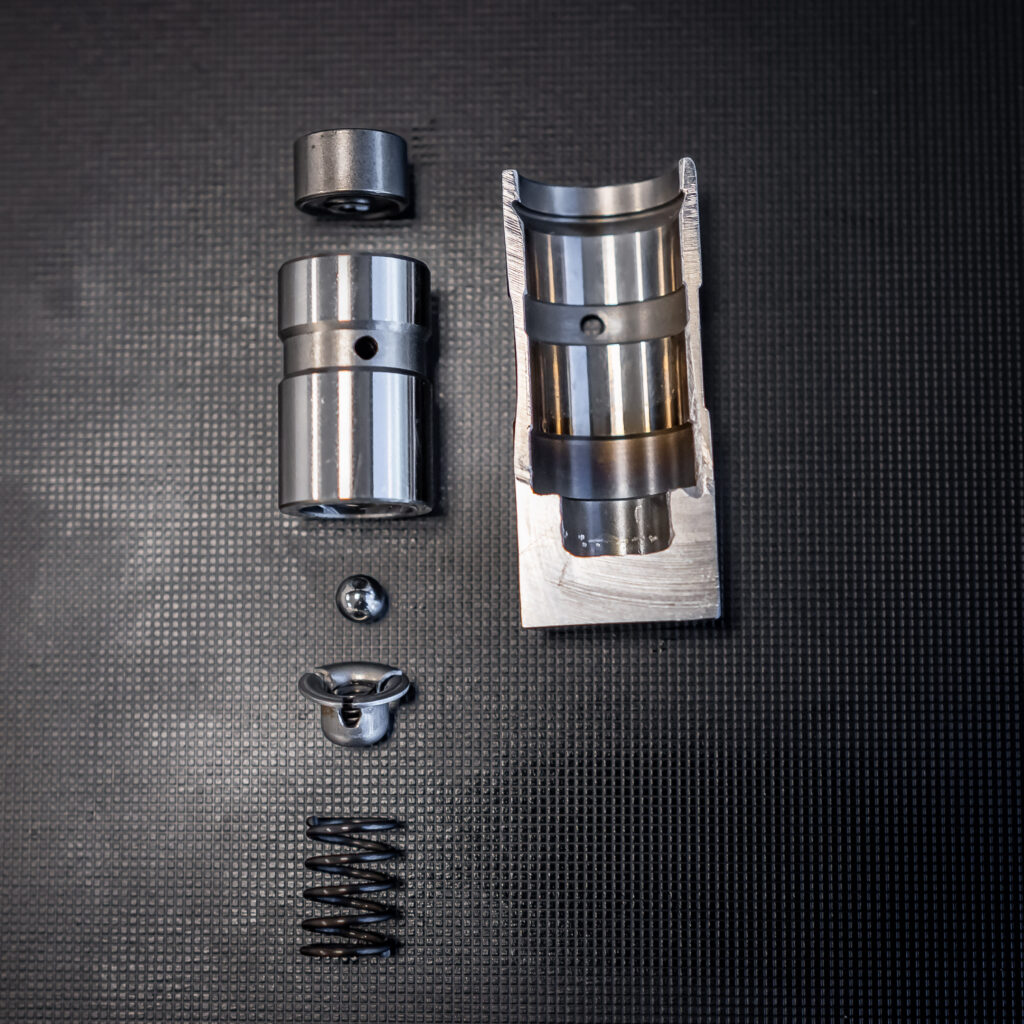
The Aftermarket’s Challenge
The aftermarket can build a better lifter; that hasn’t been a problem. However, the challenge has been how to do it economically for the average consumer. A lifter requires precision manufacturing. OEMs keep the costs down by making millions of a particular lifter at a time. Even large aftermarket companies like COMP Cams don’t even come close to the OEM production volume, so the cost of making a superior product becomes a barrier for the everyday customer.
With that problem in mind, COMP engineers had to find a solution and started from a blank canvas to design an all-new part developed to meet the demands of modern street and performance engines. The clean-slate design resulted in a highly precise lifter that is also serviceable by the consumer. We met with Valve Train Engineering Manager Chris Potter to talk about COMP’s new Evolution Lifters to hear how they tackled the challenge and what makes them so different from anything else on the market.
Evolution Lifters
COMP Cams Evolution lifters are a type of hydraulic roller lifter designed for high-performance engines built for the most popular engine families. These lifters feature a patented design that includes a precision-machined body, a larger bearing surface, and a high-strength alloy construction that ensures optimal strength and durability. At first glance, they may look like a typical hydraulic roller lifter. However, once you look closer, you can see why these lifters are revolutionary (or is it evolutionary?).
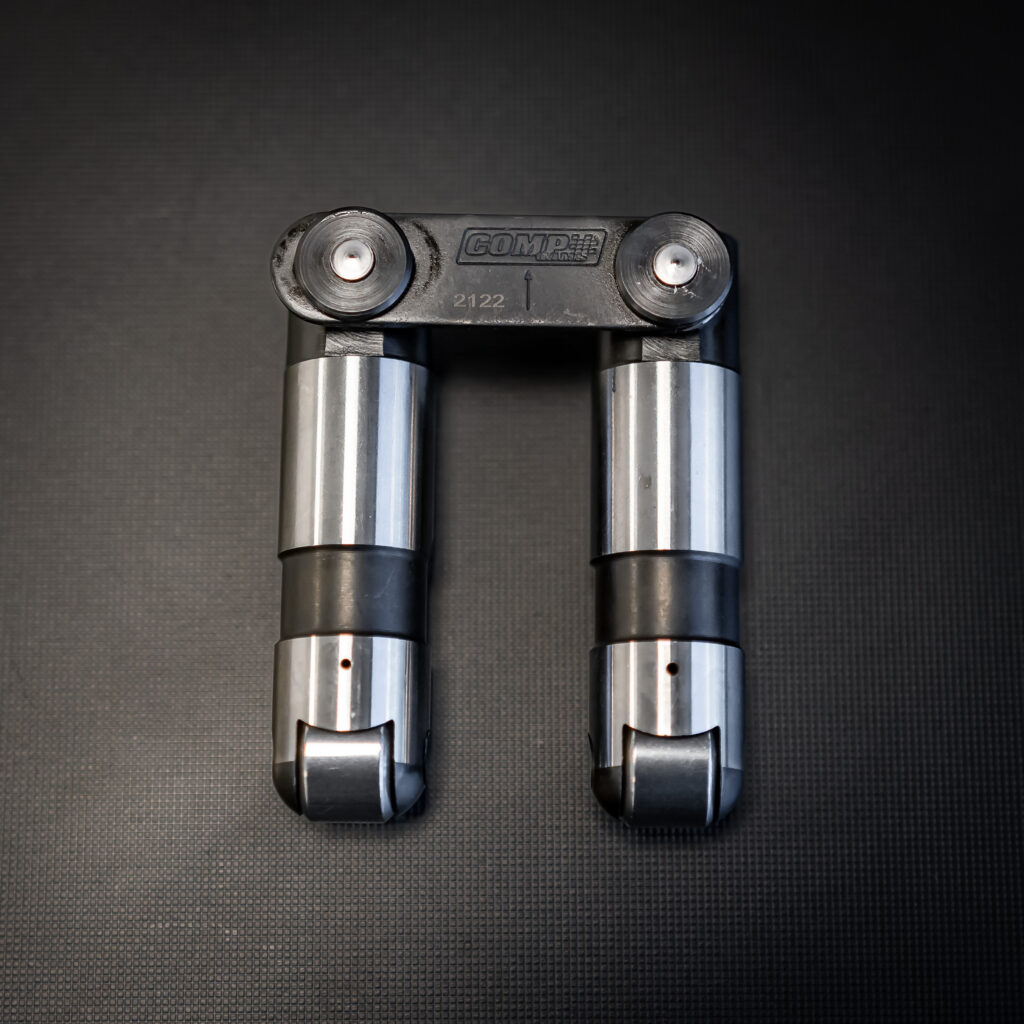
“The biggest complaints people make about stock hydraulic lifters are bleed-down [ticking] and loss of power, especially in the upper-RPM range,” Potter says. “We designed the Evolution Lifters to overcome some of those shortcomings, with consistency and reliability in mind. What we’ve done here is develop an entirely new system that separates the high-precision components of the lifter from the body of the lifter.”
HCT
Potter explains that Evolution Lifters are very different from standard lifters because of their patented Hydraulic Cartridge Technology (HCT). HCT is a self-contained hydraulic cartridge that sits within the thick wall of the roller lifter body. Think of it as a lifter inside of a lifter.
The hydraulic cartridge is the same no matter what engine family you put it in, whether it be Chevy, Dodge, or Ford. However, the lifter body is specific to the engine family, with optimized oil bands for each. Much like the move from no lifter to solid and solid to hydraulic back in the early days, HCT is yet another level of refinement in lifter technology — an evolution, if you will.
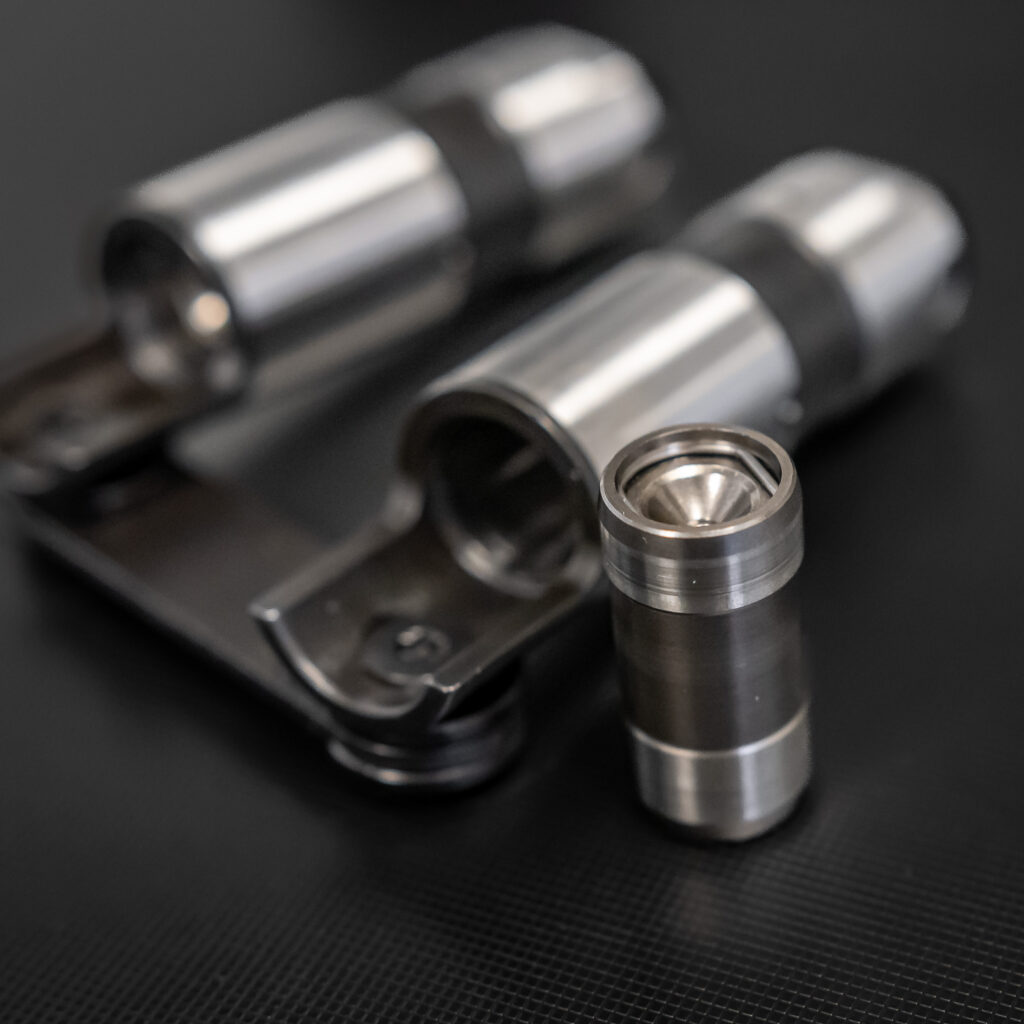
In a traditional hydraulic lifter, the inner bore of the lifter is part of the high-precision component of the hydraulic assembly. This would be the surface against which the piston (that travels up and down) would seal. However, the tolerances are so tight that if something causes the lifter body to distort, it can easily lock up a piston and cause the hydraulic lifter to fail.
With the Evolution lifter, the inner bore of the lifter body is no longer a high-precision component of the hydraulic assembly. The parts that require such high precision are all contained within the cartridge. This introduces a new degree of protection for the hydraulic elements. There are several advantages to this design that make it a revolutionary product.
1. The cartridge is serviceable, allowing anyone to service them at home.
2. The smaller oil volume in the high-pressure chamber of the cartridge allows it to be filled faster and defends against bleed-down.
3. The increased wall thickness is 18 percent stiffer than a conventional lifter for less distortion from higher spring loads.
4. Oil bands on the outside of the lifter body are optimized for each engine platform.
5. Edge-orifice oiling provides extra oiling to the lifter axle/wheel and cam interface.
6. A long wheel skirt provides extra stiffness and support in the lifter bore.
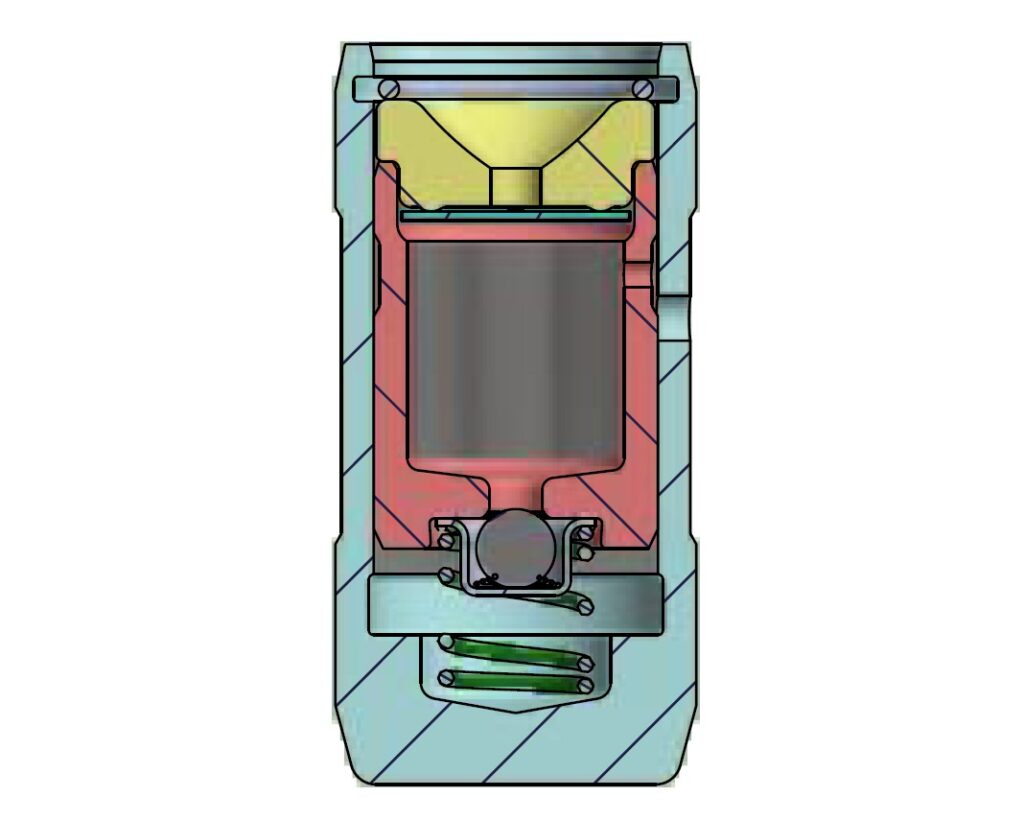
Above is a 3D CAD cutaway drawing of the inside of the cartridge. If you compare this to the CAD drawing of a traditional lifter, they look similar, but the cartridge is much smaller, so it works with much less volume. COMP took great care to ensure that the new cartridge is designed to work with modern camshaft profiles and performance valve trains, including modern spring loads, valve masses, and RPM.

The smaller cartridge volume creates one of the most responsive and quietest lifters on the market, with more consistent bleed-down rates. The tighter tolerance between the lifter body and cartridge reduces oil aeration and directs oil where it needs to be. They are available as a stand-alone drop-in lifter or with a tie-bar.
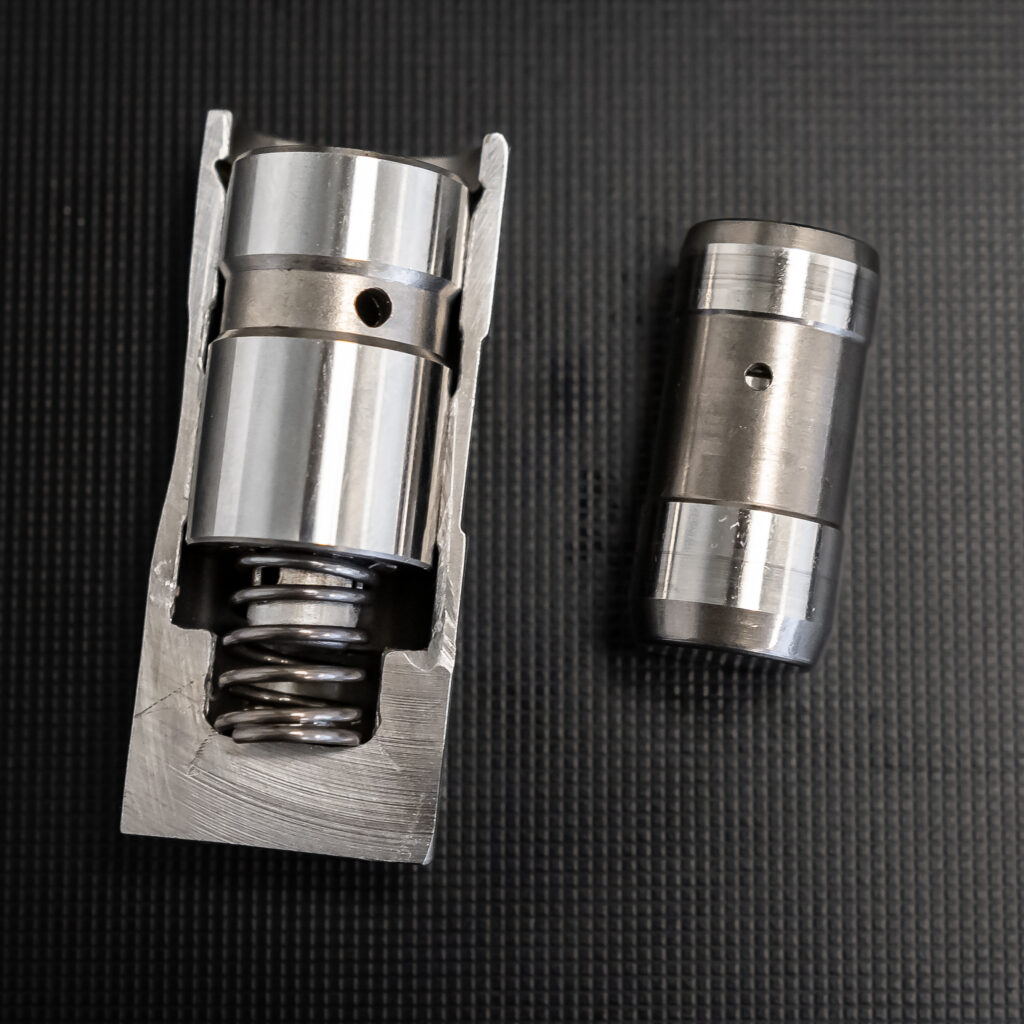
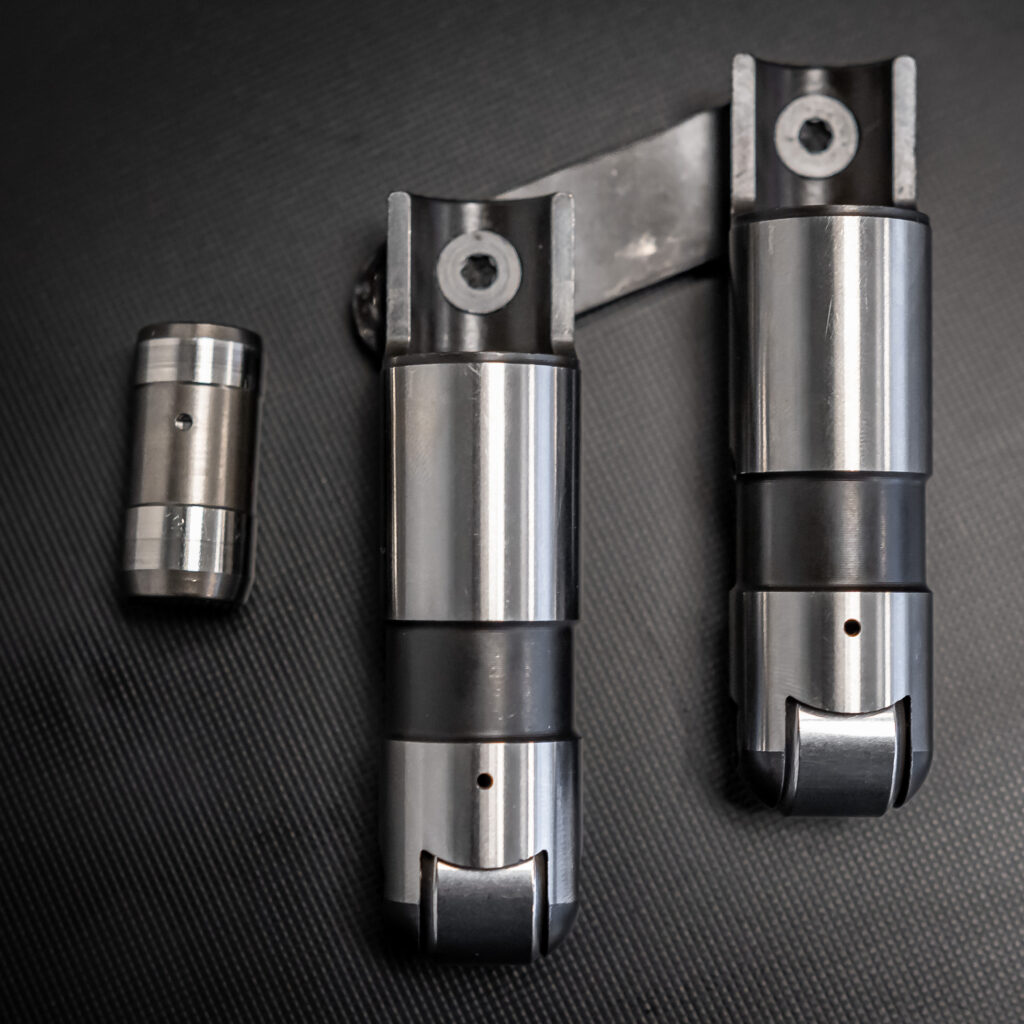
Evolution Lifter Body
Though the cartridge is a technological breakthrough, COMP engineers didn’t stop there. As mentioned earlier, they also made some advancements regarding the lifter body. Because of the cartridge’s small diameter, an Evolution Lifter’s walls are 18 percent stiffer than a conventional lifter to defend against distortion. A longer wheel skirt provides extra stiffness and support to the lifter bore, while edge-orifice oiling provides extra oiling to the lifter axle/wheel and cam interface.
However, the big news for the body is that engineers were able to map out the oil galley locations in relation to the lifter for all of the different engine families. This allowed them to optimize the lifter oil band for each engine platform to ensure a consistent oil supply from the base circle to max lift. Every engine application is capable of at least .450 inches of lobe lift. For LS engines, they were able to increase the overall height of the lifter to ensure it can run .675 inches of valve lift without falling out of the stock trays, giving it maximum performance.
Evolution Testing
The beauty of the Evolution Lifter is the repeatability of the cartridge. COMP engineers don’t have to “reinvent the wheel” for each engine type. The lifter bodies themselves are specific for the engine they are going in, with oil bands optimized for the engine family. Every single cartridge is the same and goes through testing before it is mated to the lifter body.
Obviously, much research and development went into creating the Evolution Lifters, but that means nothing without testing. As mentioned, every cartridge is tested before it is ever introduced to the body and put in a box. Specifically, the cartridge’s bleed-down rate is measured. It is pumped up, a load is placed on it, and they ensure it goes through its expected travel range within the desired time limit.
COMP Cams extensively used its Spintron, testing out the Evolution lifters. They have run them through tens of millions of cycles without issue. The majority of testing was durability assessments on LS valve trains (known to be light and stiff) and big-block Chevy valve trains (known to be heavy and flexible). The R&D shop truck is also a test mule for the Evolution Lifters and has approximately 40,000 miles of hard abuse.
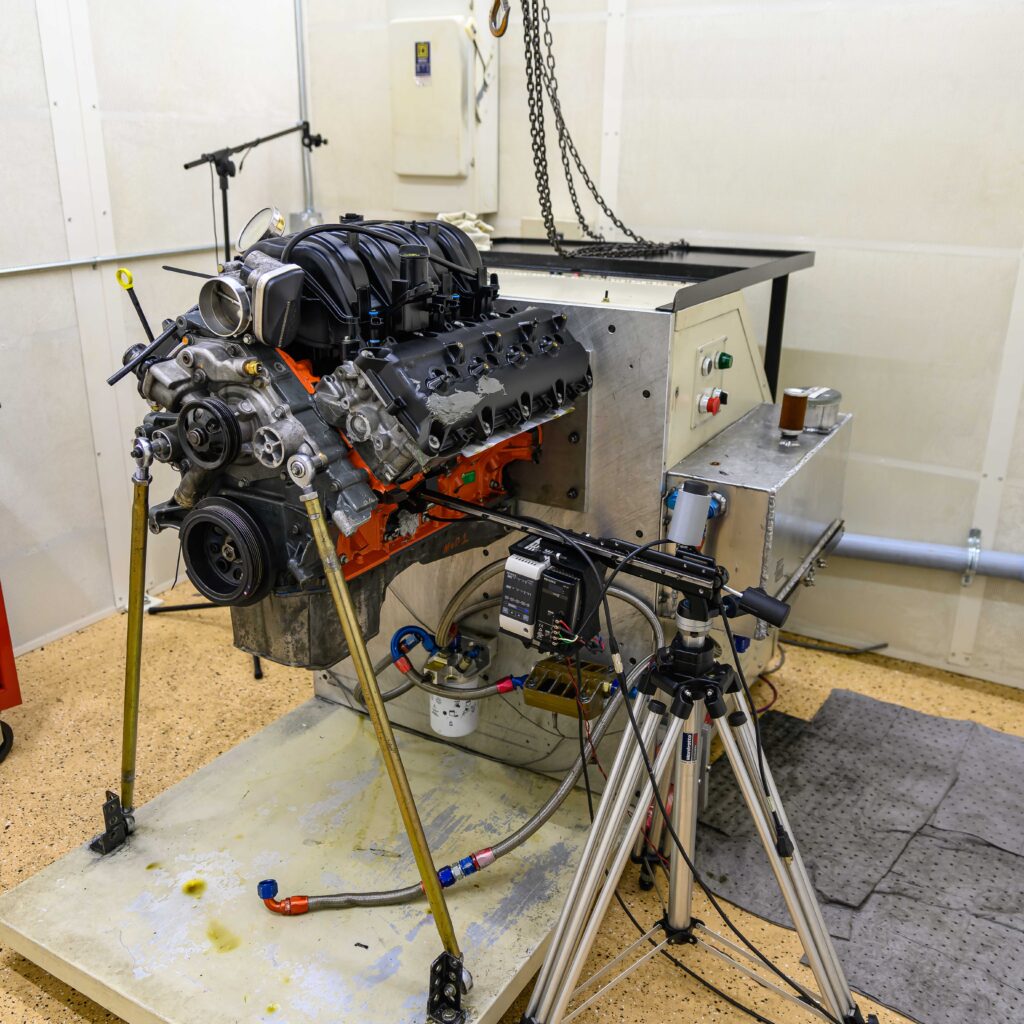
Real World Testing
All the manufacturing testing in the world doesn’t mean anything to the guy on the street if it doesn’t perform. Although there are thousands of Evolution Lifters in engines worldwide, we have a couple of real-world examples from Drag Week to whet your appetite. Both ran the 2022 Hot Rod Drag Week and competed in the 48-car Street Race Small Block Power Adder class. Run on an 8.50 ET limit (index), the SR/SB/PA class is governed by bolt-on suspension parts, a full frame, and a complete interior with an 8.50 certified rollcage.
Mark Campbell – 1995 Ford Mustang
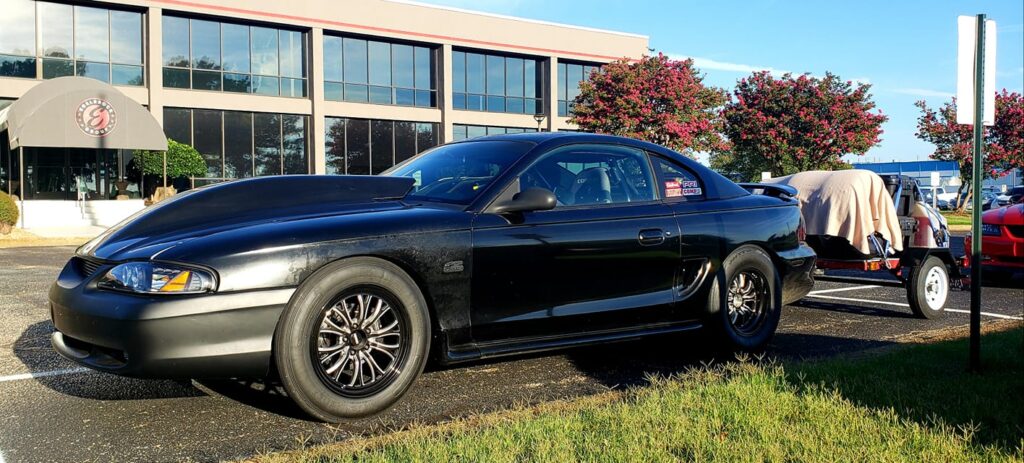
The first example is our own Edelbrock Group Vice President of Sales and Marketing, Mark Campbell. He made his Drag Week debut in 2022 with a 1995 Ford Mustang powered by a twin-turbo 427c.i. RHS LS engine. Mark led after the first two days but ended up finishing third in the class, just .06 out of First.
Mark says the lifters ran flawlessly over the 900-mile journey. “The ultraquiet operation of the lifters on the road for 900 miles was awesome, but being able to run the engine to 8,000 rpm pass after pass without worries was priceless,” Campbell said about the Evolution’s performance.
Mark never even cracked the valve covers open during the entire trip and made eight total passes for the week (two test runs and six total passes). He exceeded his goal of making it to the finish and coming in the top five. This year, he hopes to be top of the podium.
Steve & Dustin Trance – 2005 Ford Mustang
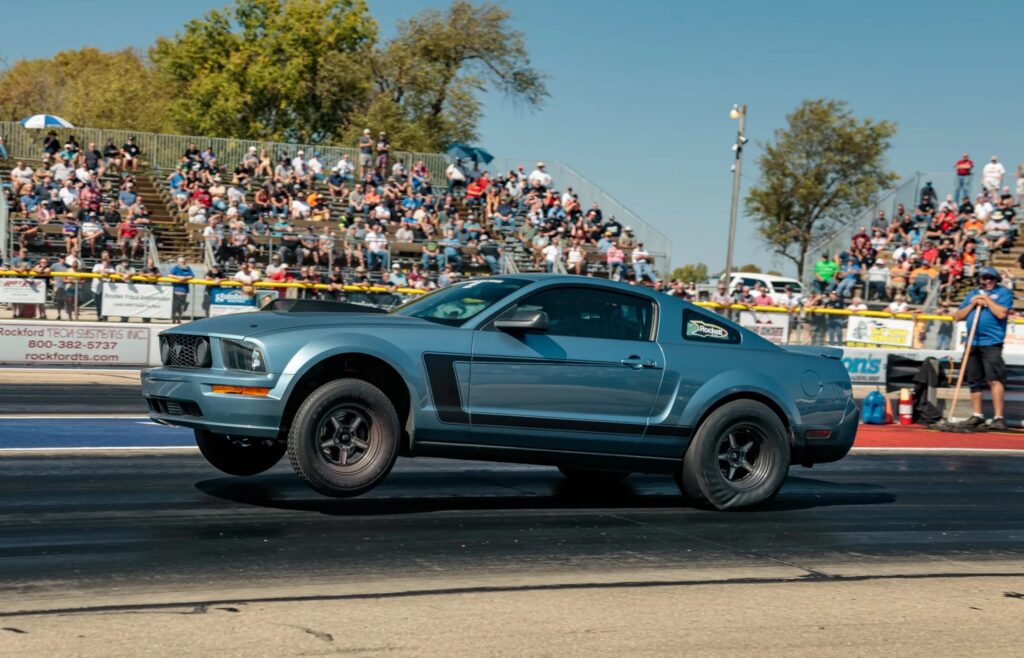
Speaking of the top of the podium, our next example did just that. For the second year running, the father and son team of Steve and Dustin Trance won the SR/SB/PA class in their 2005 Ford Mustang powered by a twin-turbo 419c.i. LSX swap. During Drag Week 2021, Steve had some concerns with lifter tick at low RPM. He minimized it by playing with the preload, and they survived the week. But while freshening up the engine over the winter, he was intrigued by the Evolution Lifters and decided to give them a try for DW2022.
During testing, he was impressed with how quiet the Evolution Lifters were. When the rubber met the road on the strip, the Trances were extremely happy with a trouble-free valve train after the abuse they put it through during the week. Being veterans of Drag Week, they understood the importance of getting as close to the index as possible.
Dustin was remarkably consistent and even hit a perfect 8.500 pass at Byron. The team reduced the overall winning class average to 8.514 seconds. However, to hit that mark and beat second place by just .02 seconds, they made a total of 22 passes! They certainly leaned on the engine to achieve the win, but they never had any trouble out of the lifters. That is a testament to the engineering that went into designing the Evolution Lifters.
Conclusion
Being able to achieve repeatable passes within a few hundredths after driving 900 miles, with track and weather conditions changing daily, shows the build quality of these engines. Having a hydraulic roller lifter like the Evolution Lifters assured both teams that the COMP engineers did their homework regarding reliability and consistency.
If you want longevity and consistency, you would be hard-pressed to find a better option with more precision capability than the Evolution Lifters. They are well worth the slight cost difference over a conventional hydraulic roller lifter. Though they are a bit more expensive on the front end, the ability to rebuild them instead of buying an entirely new set will offset the cost in the long run.