Everyone knows Edelbrock is the leader in aftermarket aluminum intake manifolds, water pumps, and cylinder heads. Some know those aluminum parts are cast in Edelbrock’s own foundry in San Jacinto, California. But did you know that the Edelbrock Foundry does way more than just make parts for Edelbrock?
Well, they do! And they make things that do not even have to do with the automotive market. The Foundry is capable of casting just about anything out of aluminum (at least up to a certain size). However, the Foundry doesn’t just melt and pour aluminum into molds. The Edelbrock Foundry’s services include concurrent design engineering, prototyping, traditional and CNC pattern making, tooling production, core production, green and dry sand molding, solution heat treatment, finishing, and machining.
A foundry is not the world’s sexiest place to work, but to people interested in how things are made, it can be an intriguing place. We thought we would give those of you who may not know what a foundry is or how it operates a little education on the inner workings of the Edelbrock Foundry. We met with General Manager Charles Emerson and Director of OEM and Foundry Sales Robert Morse to tell us about the unique capabilities of the facility and how it operates. But first, a little background.
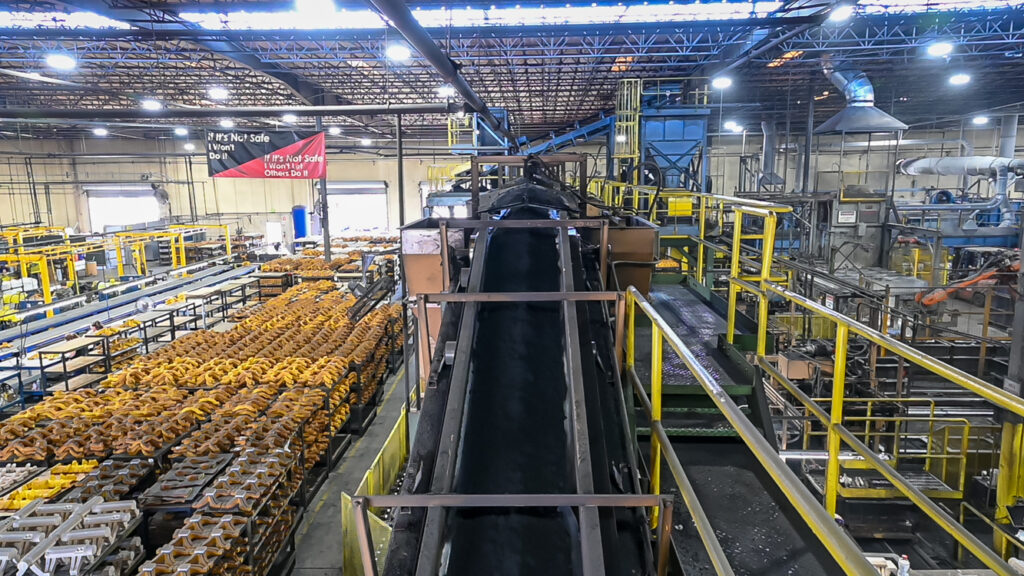
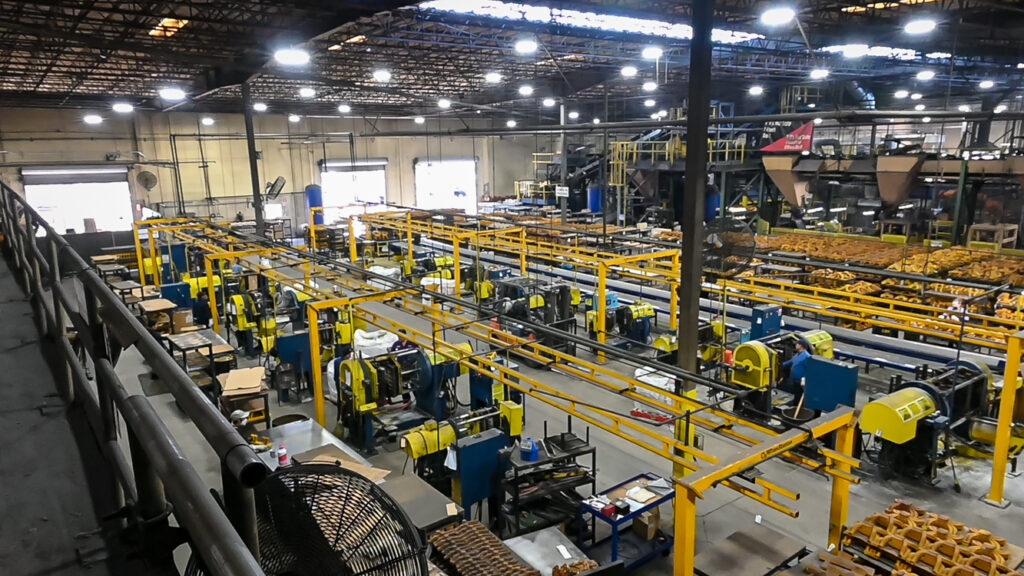
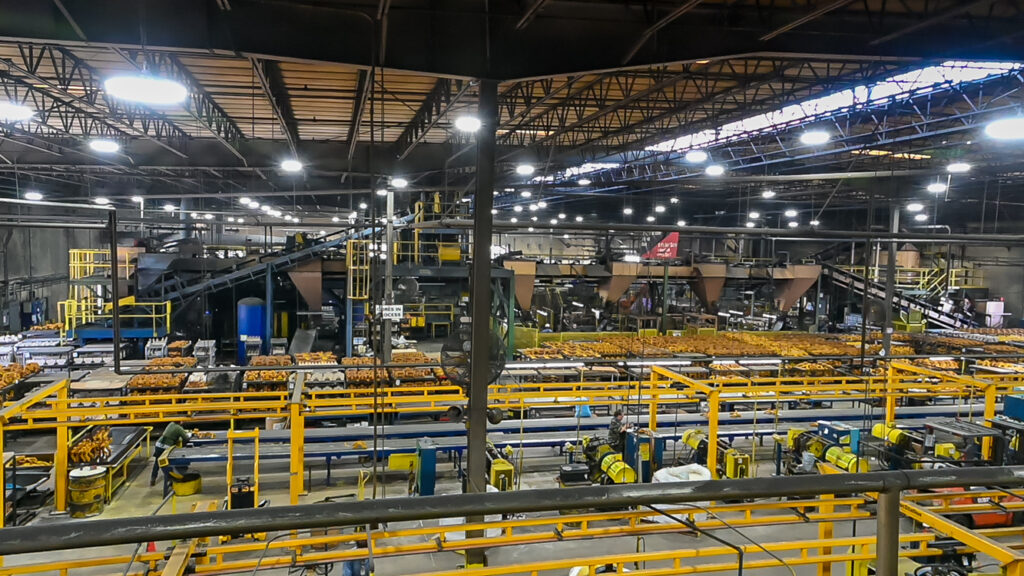
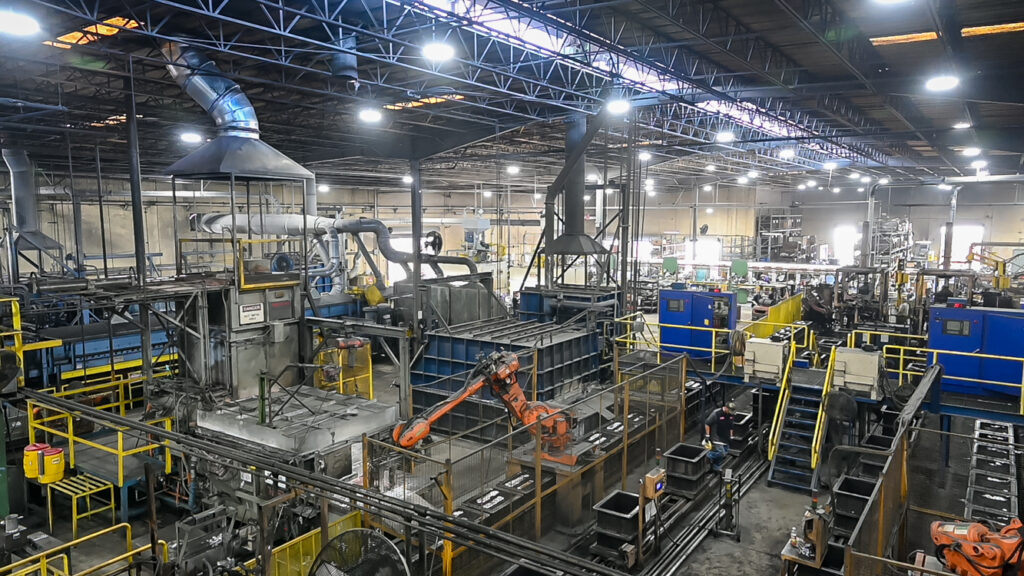
Foundry Terms
To understand what the Edelbrock Foundry does and what it is capable of, we need to define some of the terms, products, and processes used in the industry for those who may not be privy to casting manufacturing.
Pattern — A pattern is a model of the final casting that is used to make a mold. The pattern is made to be slightly larger than the final casting to allow for shrinkage of the metal. It also has features that allow it to be removed from the mold.
Mold — A mold is a cavity that is used to cast the outside shape of a final part. It is the negative shape of the pattern. Edelbrock has a permanent mold line that uses cast iron, and two types of sand mold lines (dry and green). The mold is removed from the final casting.
Core — A core is a one-time-use insert that is used to create internal passages or features in a casting. It is placed inside a mold and gets shaken out at the end of the casting process.
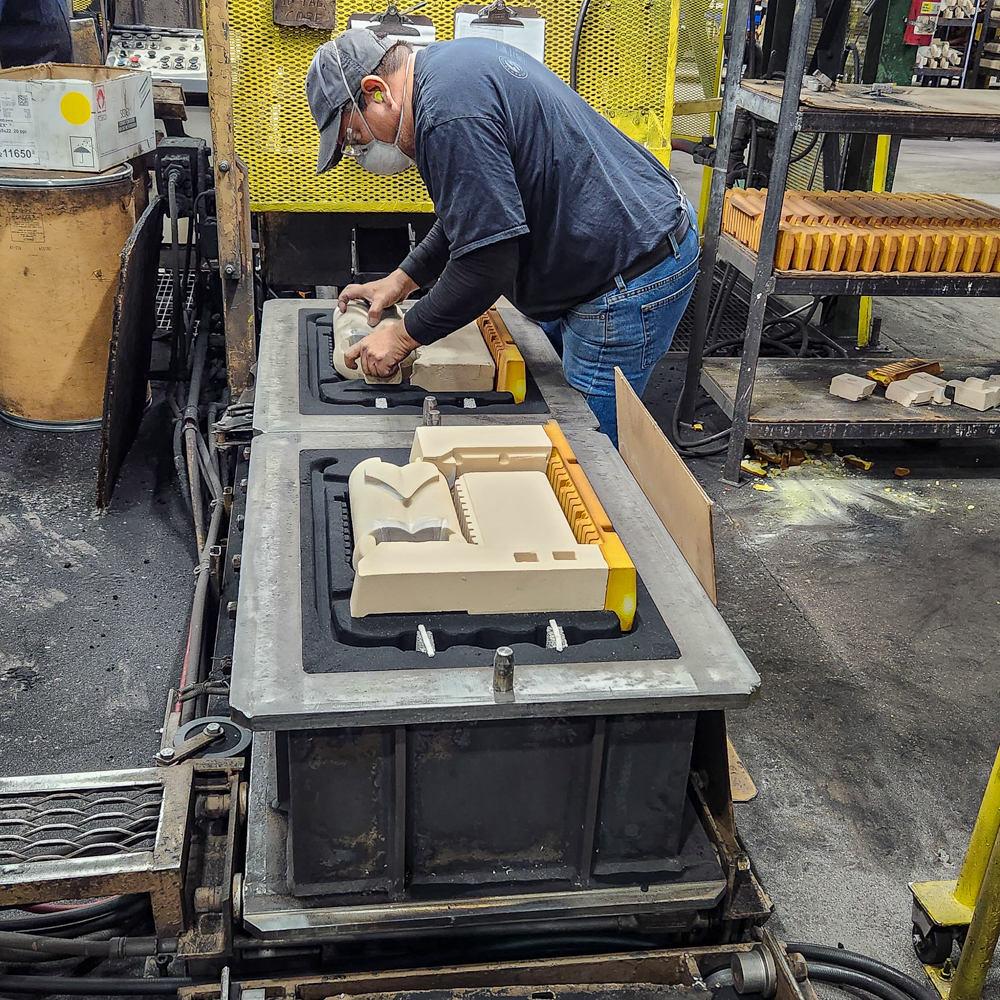
Concurrent Design Engineering — also known as concurrent or simultaneous engineering. CDE is an approach to product design and development emphasizing collaboration and integration among different disciplines and teams involved in the design process. It aims to reduce development time, cost, and potential issues by concurrently considering various aspects of the product throughout its lifecycle.
Flask-Less Match-Plate Molding — designed to automate and streamline the process of creating molds for casting metal parts in high-volume production. In a flask-less match-plate molding machine, the mold is created using a two-part pattern (typically made of metal or resin) known as a match plate. The machine brings the two halves together in a process known as squeeze molding, binding the sand to form the mold cavity. Excess sand is removed, and the resulting mold is ready for casting.
Cope and Drag Molding — a common technique used in foundries for creating sand molds for casting metal parts. It is a two-part molding process that involves the use of a cope and a drag, which are the top and bottom halves of the mold, respectively. A pattern including features such as the outer shape of the part, core prints (for creating internal cavities), and gating system (channels for pouring molten metal into the mold) is placed in one of the halves. A special molding sand is packed tightly around the pattern before it is removed, and cores are introduced to create internal cavities or complex shapes. The cope and drag are brought back together then molten aluminum is poured in and allowed to cool before the part is shaken out of the mold.
Tower Jet Melter Furnace — The tower jet melter furnace gets its name from the vertical tower-like structure and the use of high-velocity jets of hot combustion gases for melting the metal. It is specifically designed for high-capacity melting and efficient heat transfer. Reverb natural gas furnace — also known as a reverberatory furnace, is a type of furnace commonly used in foundries for melting and holding molten metal. The term “reverberatory” refers to the design of the furnace, which includes a refractory-lined chamber where the metal is heated indirectly.
Reverb Natural Gas Furnace — Also known as a reverberatory furnace. It is a type of furnace commonly used in foundries for melting and holding molten metal. The term “reverberatory” refers to the design of the furnace, which includes a refractory-lined chamber where the metal is heated indirectly.
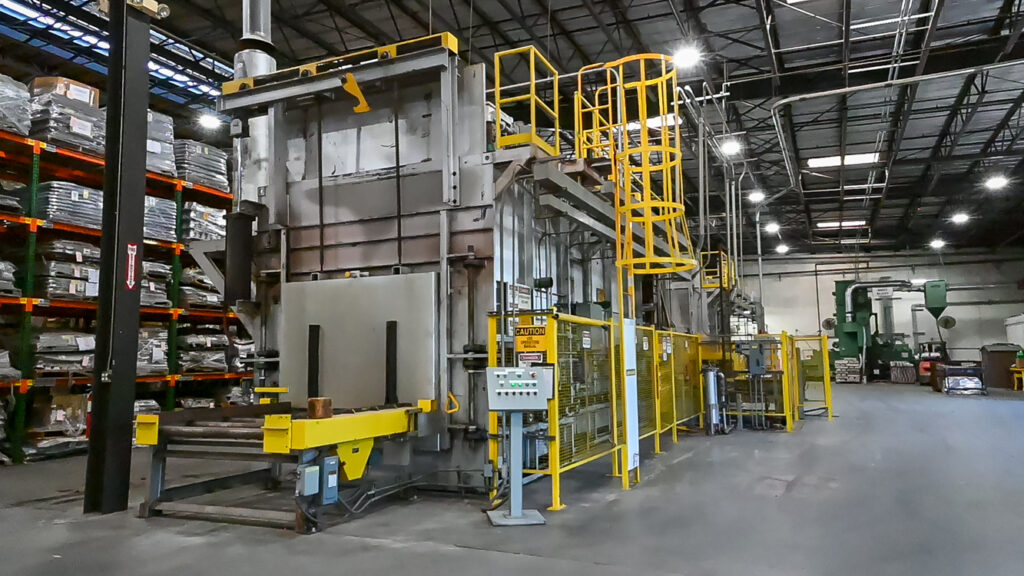
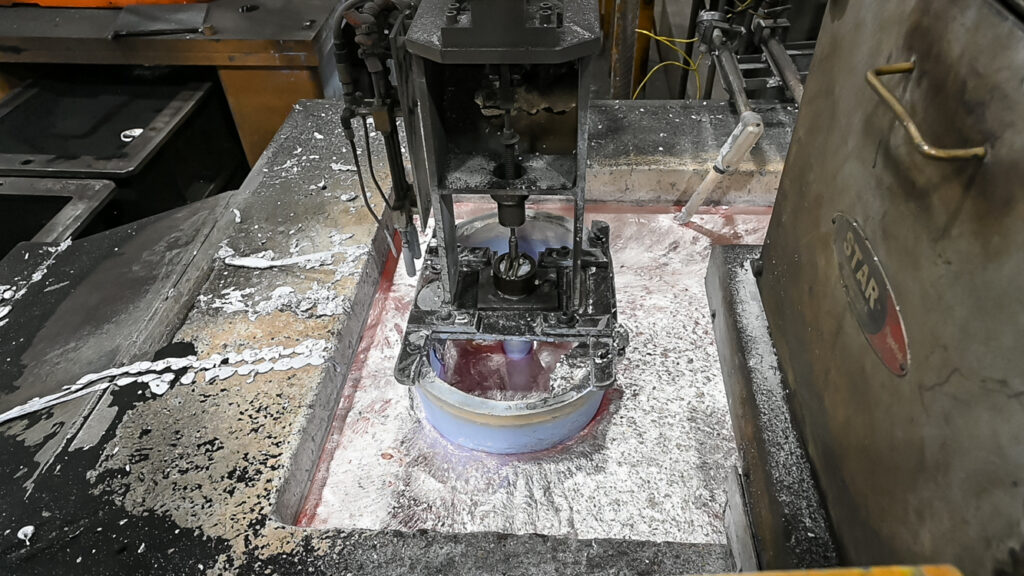
Edelbrock Foundry Background
With the volume of aluminum that Edelbrock uses, it made good business sense for Vic Edelbrock Jr. to green light building a foundry to keep parts “Made in America.” The Edelbrock Sand Foundry is a state-of-the-art aluminum casting facility established in 1990. It operates in two 73,000-square-foot buildings purposefully located in the dry air of the California desert. Humidity (or lack thereof) is a significant consideration when it comes to sand casting, and San Jacinto proved to be the perfect location.
Specializing in A356 and 808 aluminum, the foundry utilizes three different types of castings: permanent mold, dry sand, and green sand (more on each later). Though aluminum casting is the end game, the Edelbrock Foundry is a total start-to-finish solution for the Edelbrock Group and its foundry clients. From the outset, the foundry has always supplemented its core business with white-label parts for other brands and industries. You might be using an aluminum part from Edelbrock right now and not even know it.
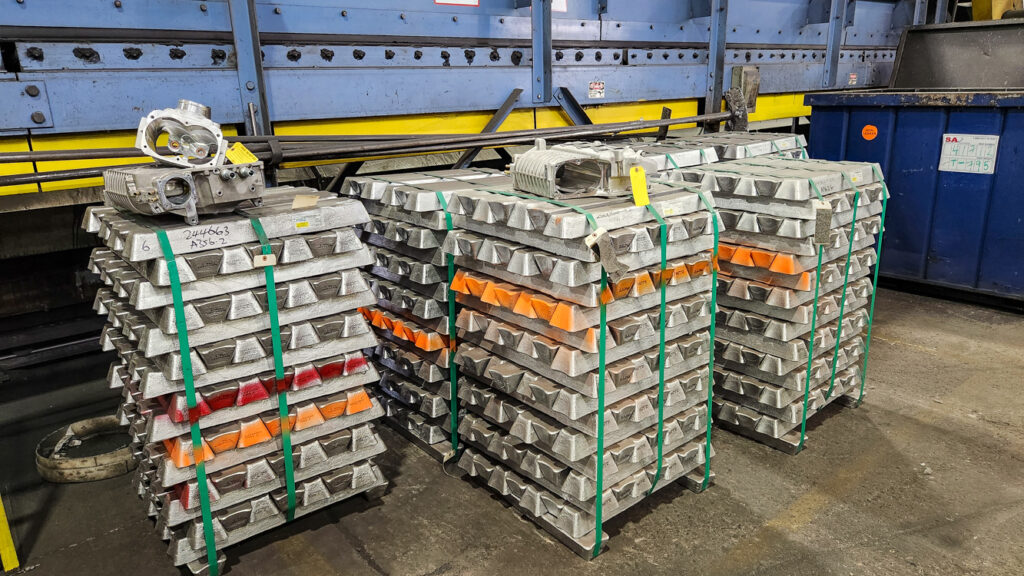
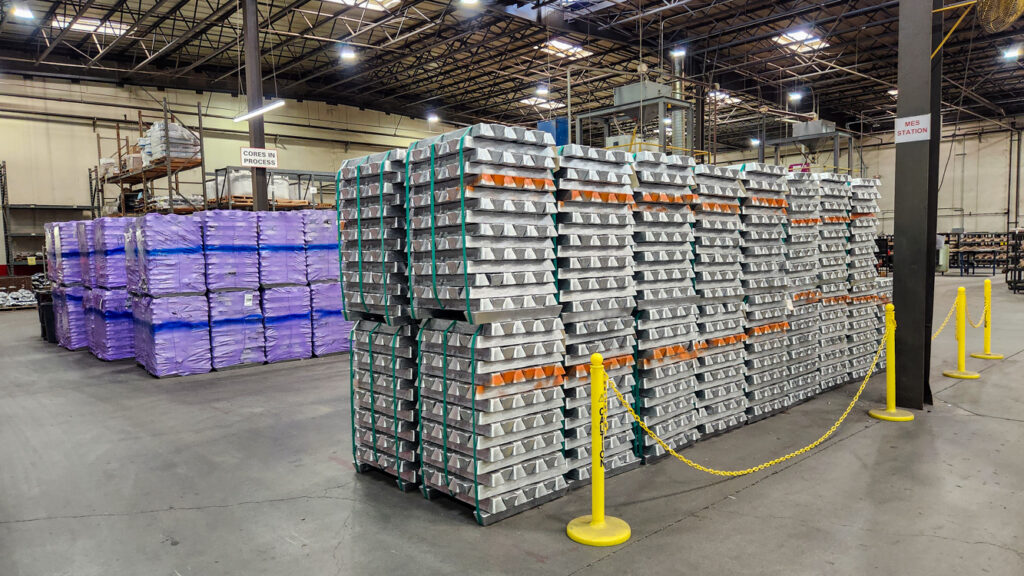
Technology At the Edelbrock Foundry
When most people think of a foundry, they think of something resembling a scene from Peaky Blinders or the Roaring ‘20s with lots of fire, steam, clanging sounds, and people covered in soot. While parts of the process can be dirty, robots now do most of the unsavory work. Gone are the days of men wearing heat-shielded suits in front of a cauldron of liquid metal. However, it is still a hot place to work. There is no way of getting around it when you are melting aluminum into liquid form.
From start to finish, technology is now the name of the game at the Edelbrock Foundry. The Edelbrock Group continues to invest in new tools and machines to help improve processes and cut client costs. The latest additions to the Foundry are a 3D printer and a deburring machine that will save time and money. A couple more finishing machines are slated for delivery in the fall.
New Machines
The 3D printer eliminates the need for tooling. The Edelbrock Foundry is the only one on the West Coast with this technology. It will significantly improve development costs and time for short-run castings and prototyping. This 3D printer gives Foundry engineers the capability to go from model to casting within two to three weeks.
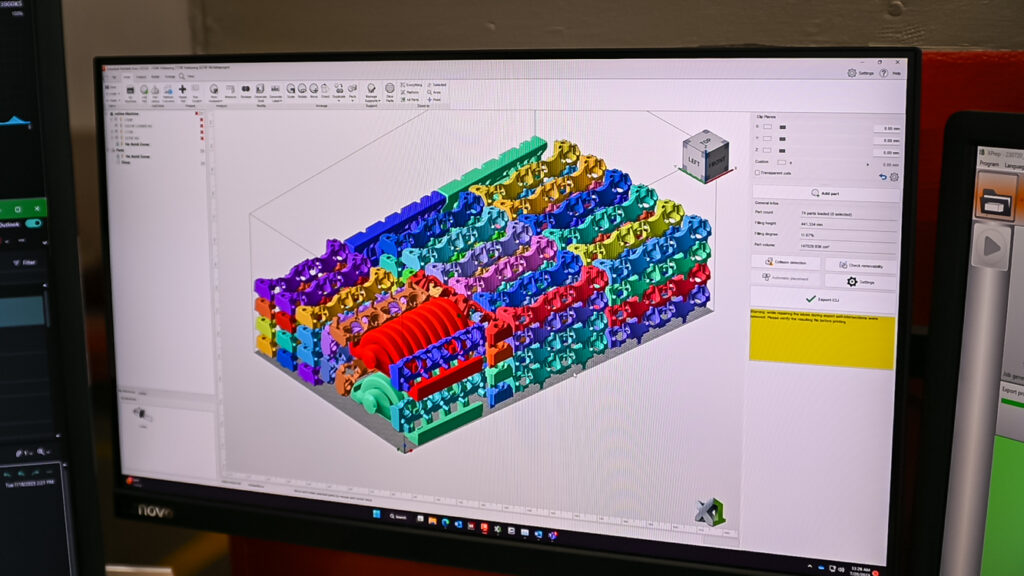
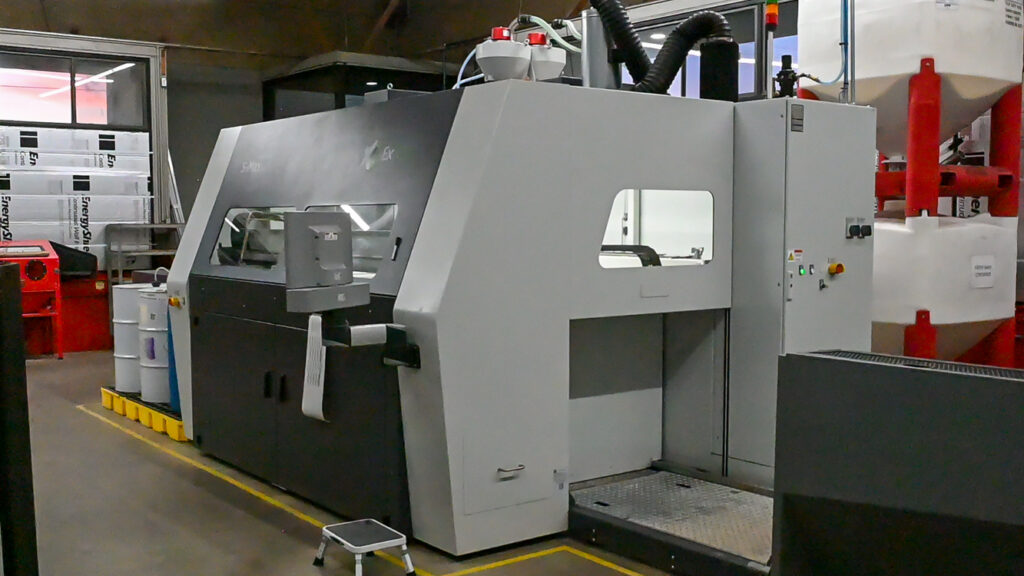
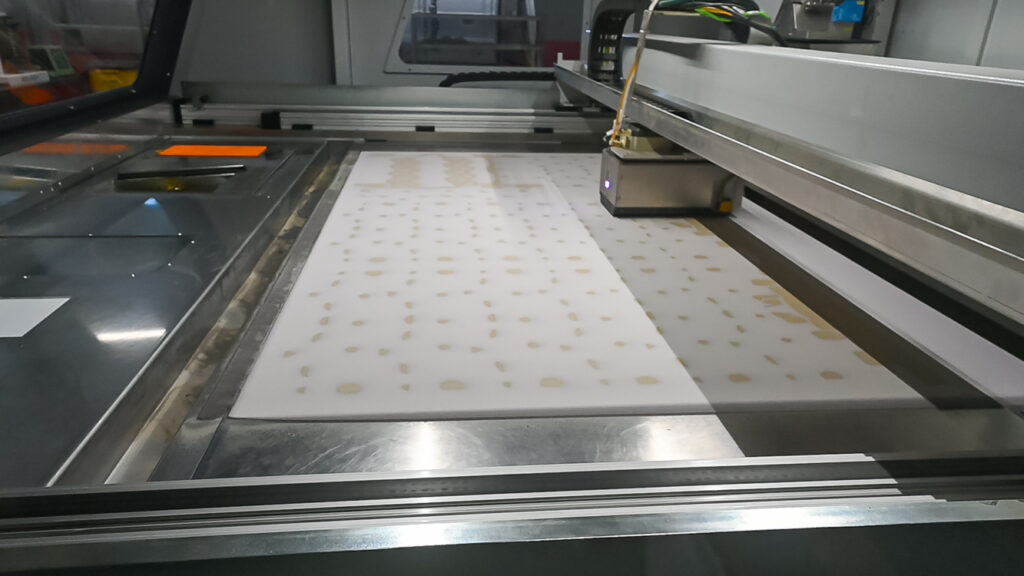
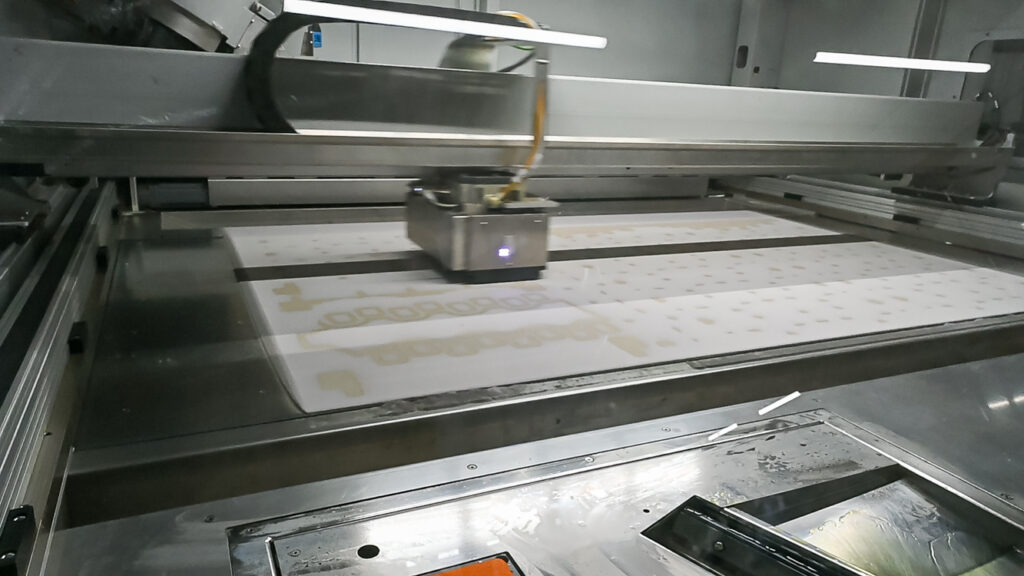
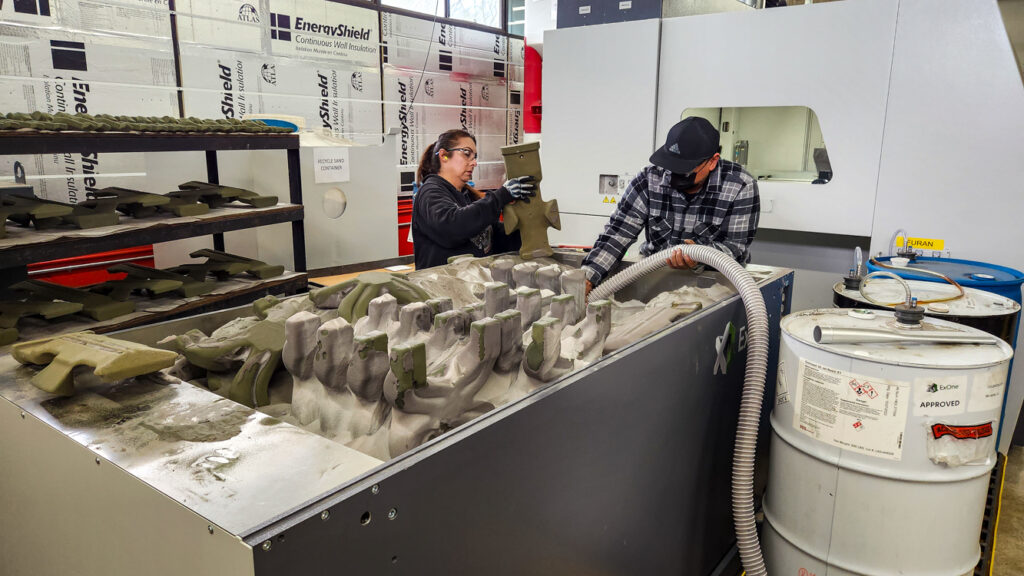
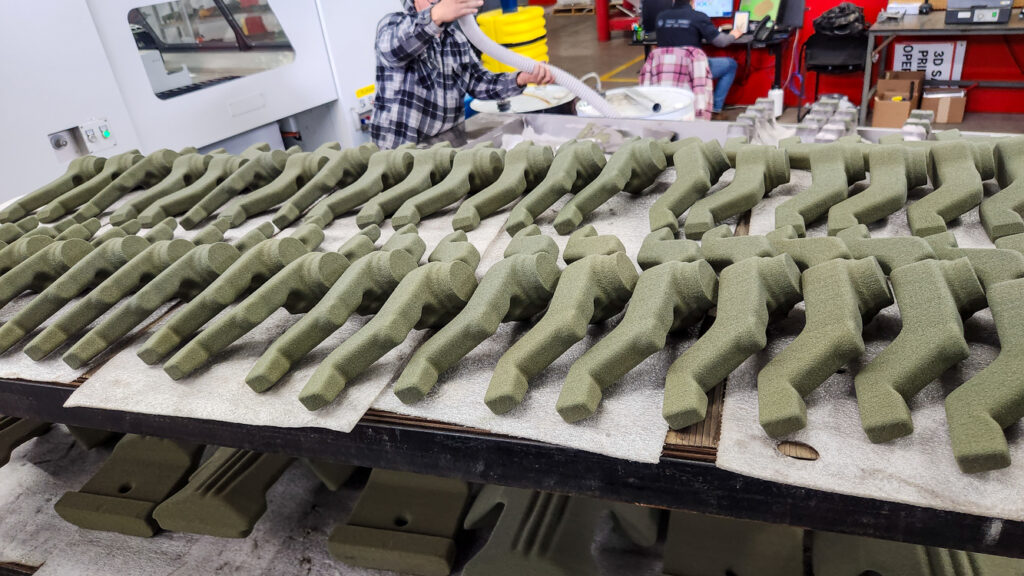
“We have the capability now of doing short-run castings with no tooling,” Emerson says. “We can do prototypes off models, so we can print a mold and pour a casting for somebody straight from a model. That includes gating, rigging, and solidification modeling — things that can take up a significant amount of resources. From the other end of the spectrum, we can put it into production.”
On the other end of the spectrum, the deburring machine will carve off time during the finishing phase. It is an automated machine that can quickly remove rough edges inherent in the casting process, which can be a significant time killer. Both of these new machines allow the Foundry to be nimbler for their customers.
One-Stop Shop for Quality Castings
Edelbrock engineers utilize a wide range of 3D modeling to build products, either from scratch or a client engineering file, for rapid prototyping, tooling production, and pattern making. Beyond that, the Foundry’s unique position and high-quality control mean engineers have the tools to provide additional services performing computational fluid dynamics, finite element analysis, solidification modeling, and metallurgical analysis.
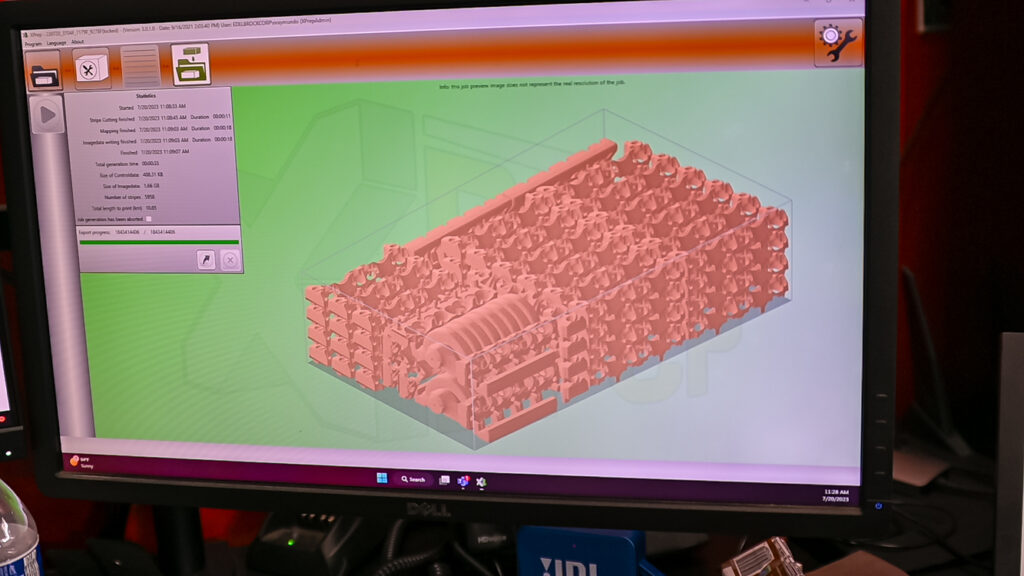
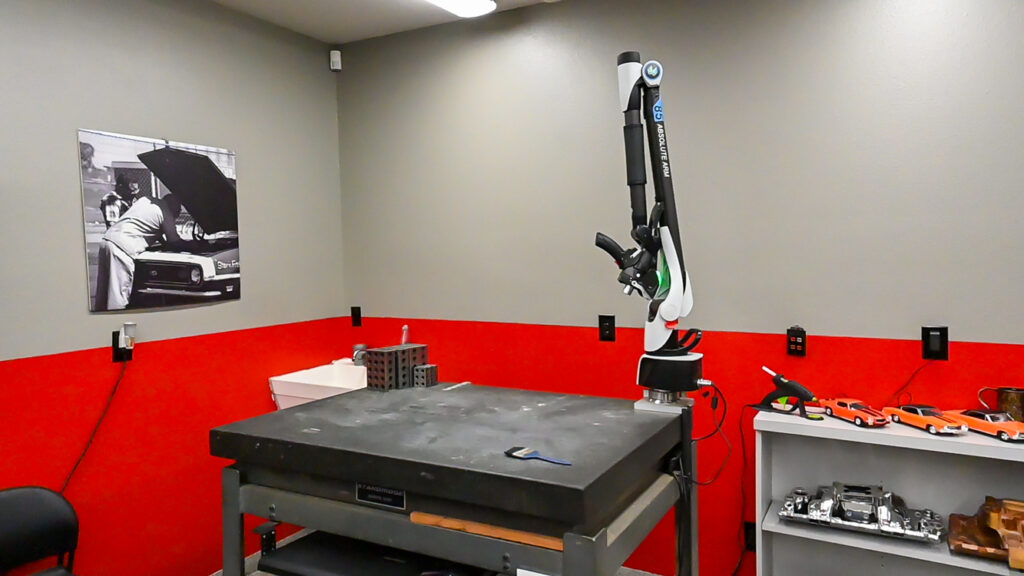
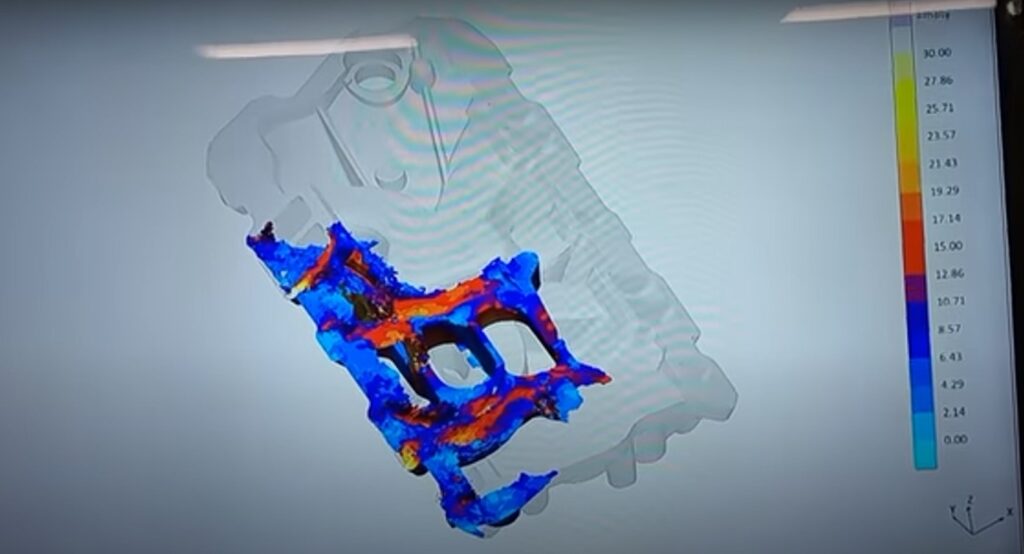
As mentioned, the Edelbrock Foundry can do about anything when it comes to casting aluminum parts, and it does much more than just Edelbrock products. Many of those are white-label parts for customers, so we cannot talk about all of them, but the industries are far-reaching. From irrigation fittings to agricultural products to freight trains and baseball pitching machines, the possibilities are endless.
The Foundry has made and continues to make parts for the OEM automotive market. One of the newest clients we can talk about is Lotus. The Edelbrock Foundry produces the supercharger for its new 3.5-liter V6 engine in the new Emira. In fact, superchargers are becoming a specialty. Everyone knows the popularity of the Edelbrock-branded superchargers, yet two of its biggest supercharger clients are in the agricultural world. The Foundry even cast the Dodge Hellcat supercharger for the first few years.
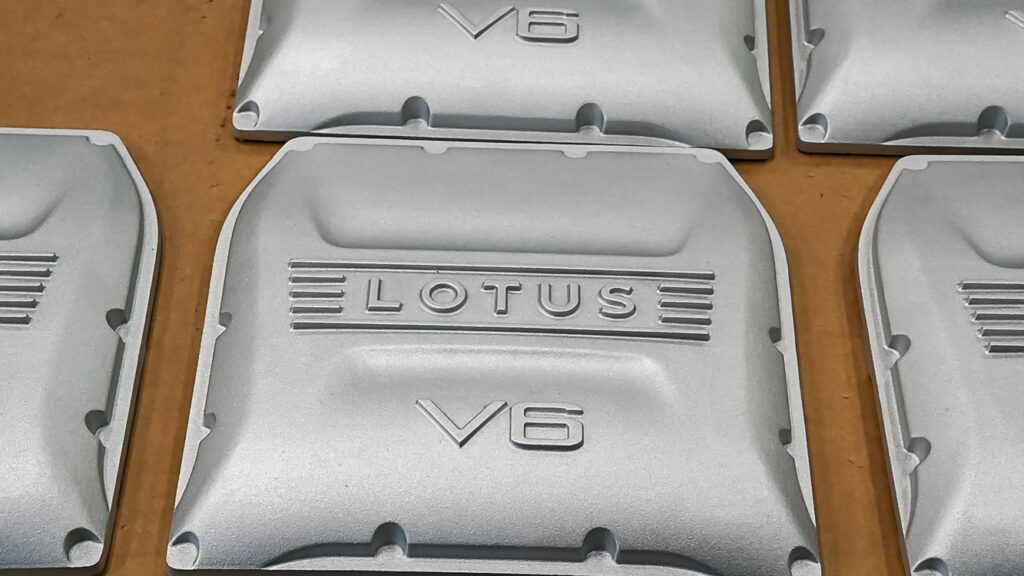
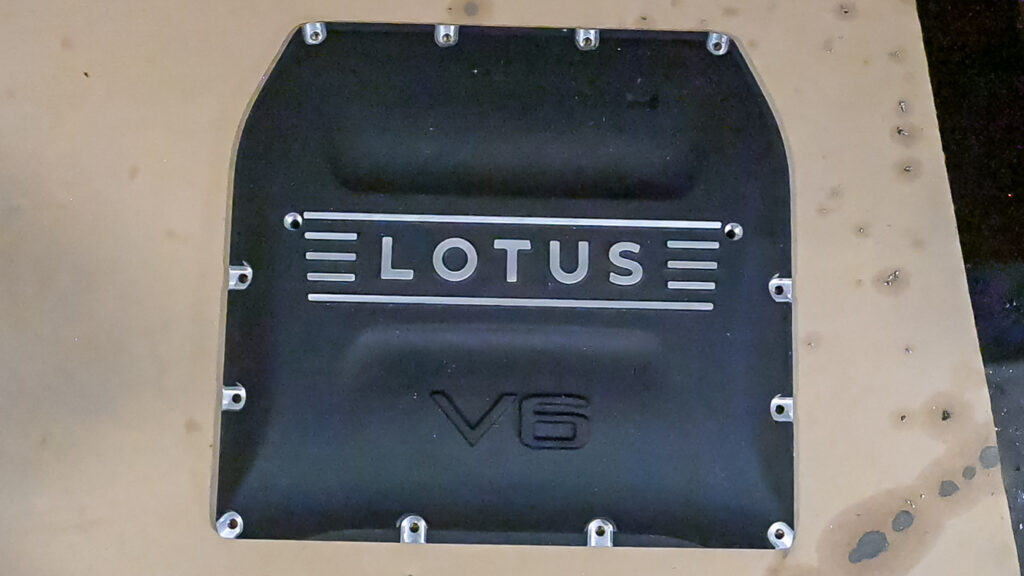
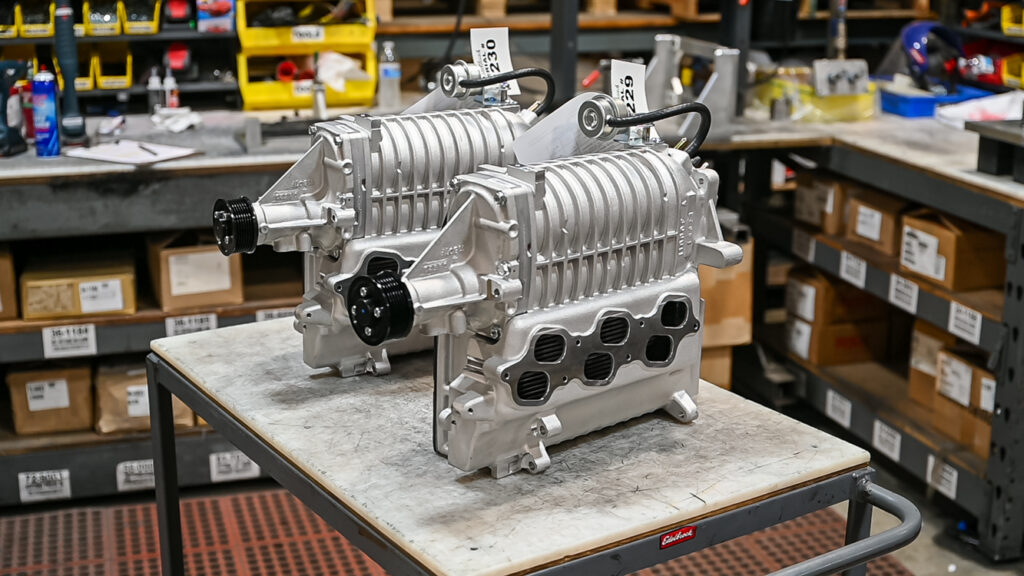
Foundry Manufacturing Processes
Technology is also present in the manufacturing process. There are three major processes that must happen before a part is cast — sand handling, aluminum melting, and core production.
Sand Handling
The Edelbrock Foundry has a self-contained sand handling system capable of processing 100 tons of sand per hour by mixing 5,000-pound batches every 90 seconds. A complex conveyor system automatically replenishes the molding machines through 400 feet of underground tunnels. A Hartley automatic controller tests each batch for proper moisture content and compaction, which is critical to proper casting.
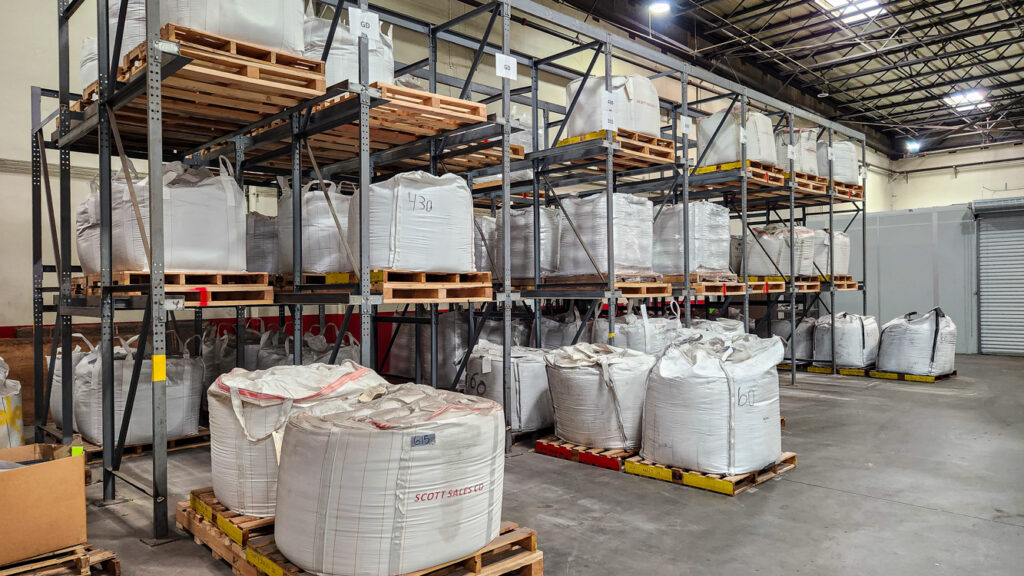
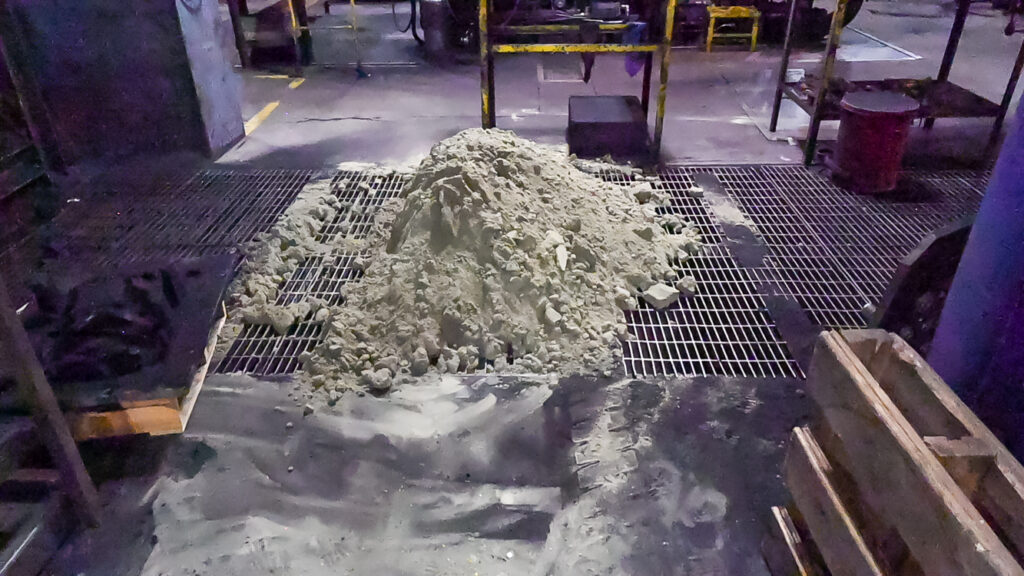
Aluminum Melting
Aluminum is melted in two modern tower jet melter furnaces. Once melted, it is held in liquid form using three reverb natural gas furnaces before casting. An interesting note is that the aluminum stays in liquid form 24 hours and day, 365 days a year, and there are alarms in place to alert the appropriate people should the temperatures drop.
Core Production
The Foundry core production is anchored by 20 core machines. Four of these are ISO-cure (cold box) machines, while the other 16 are B&P shell core (hot box) machines. The ISO-cure process involves mixing sand and a two-part binder with a gas catalyst, while shell cores are formed by filling a heated cast-iron core box with resin-coated sand. ISO-cure cores are known for their high strength and dimensional stability, while shell cores are thin-walled and hollow for creating intricate internal cavities where precision and fine details are required.
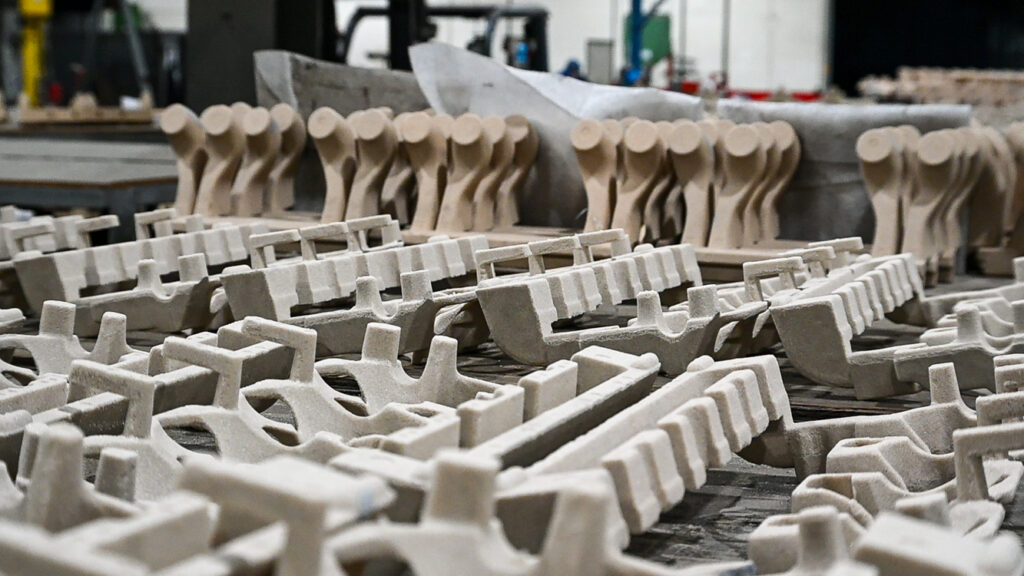
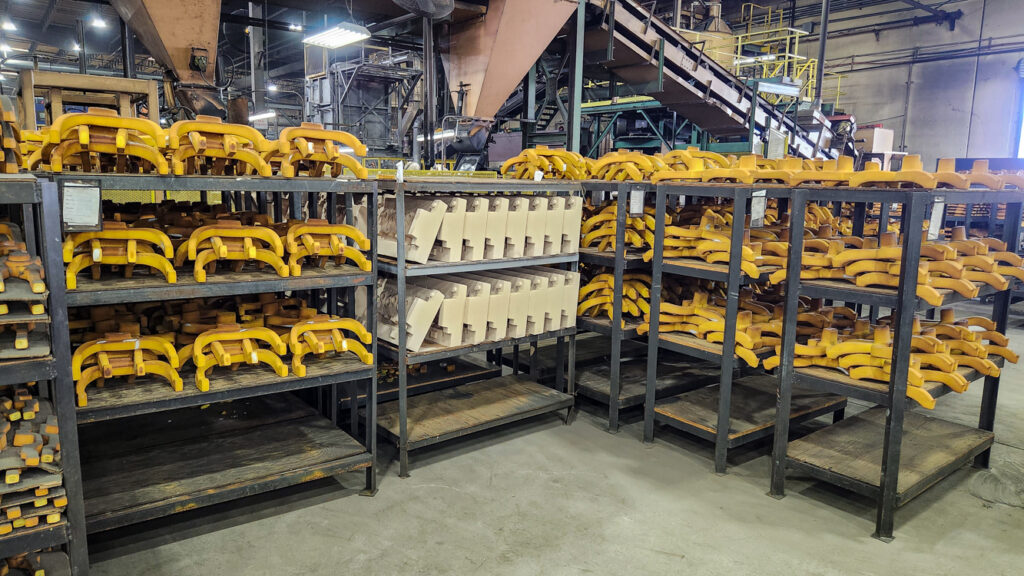
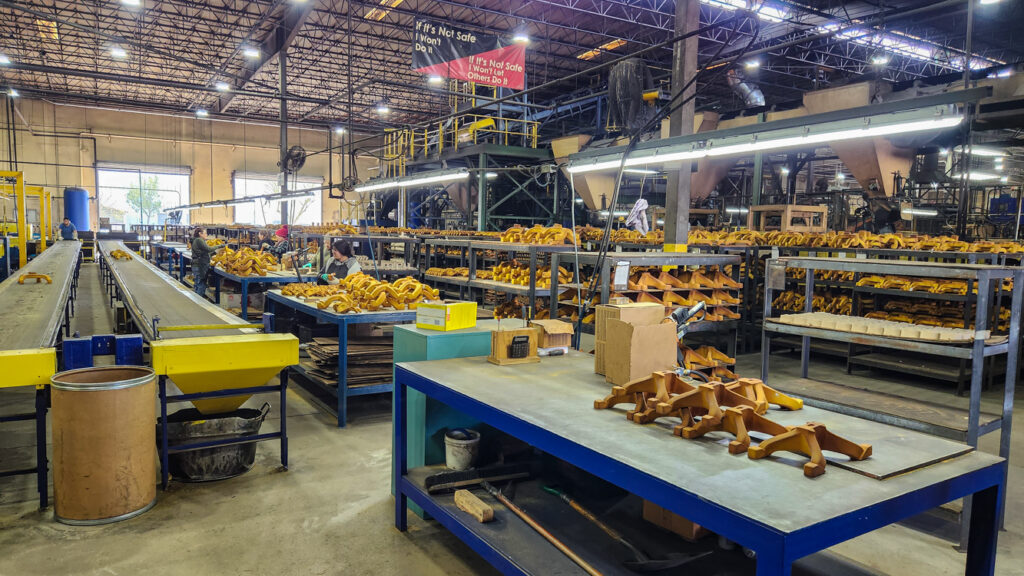
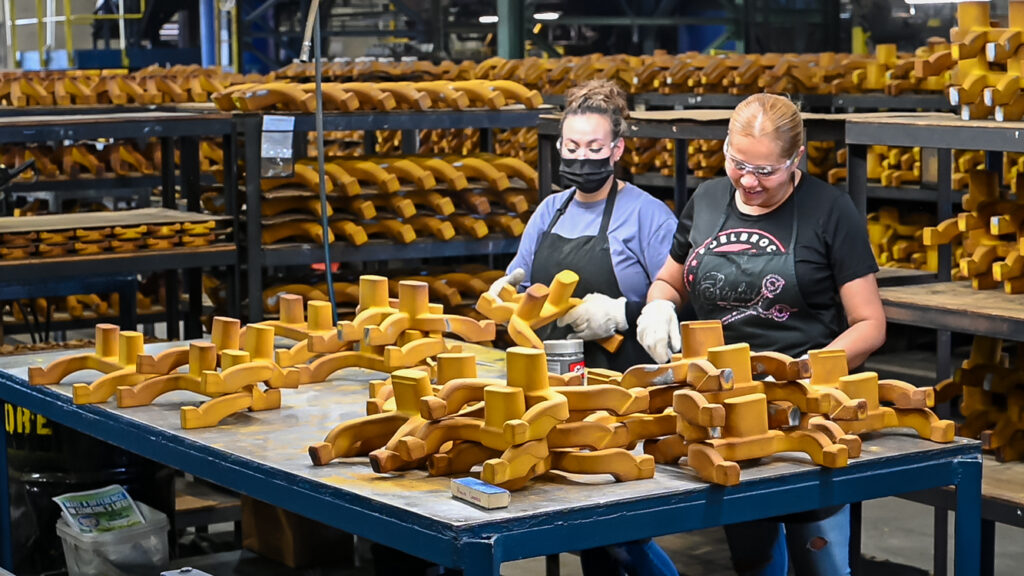
Castings
The Foundry uses three types of processes to create a casting depending on several factors, but size and/or production volume largely dictate the type of mold used. The three types are Permanent, dry sand, and green sand molds.
Permanent molds are for high-volume parts that are run consistently. Dry sand molds use a chemical binder to hold the sand together and are for short-run castings. The dry sand molds do not last as long as green molds. Green sand is actually black and is the most used process. It is called green because it only uses water, clay, and sand — there are no additives used in the bonding process.
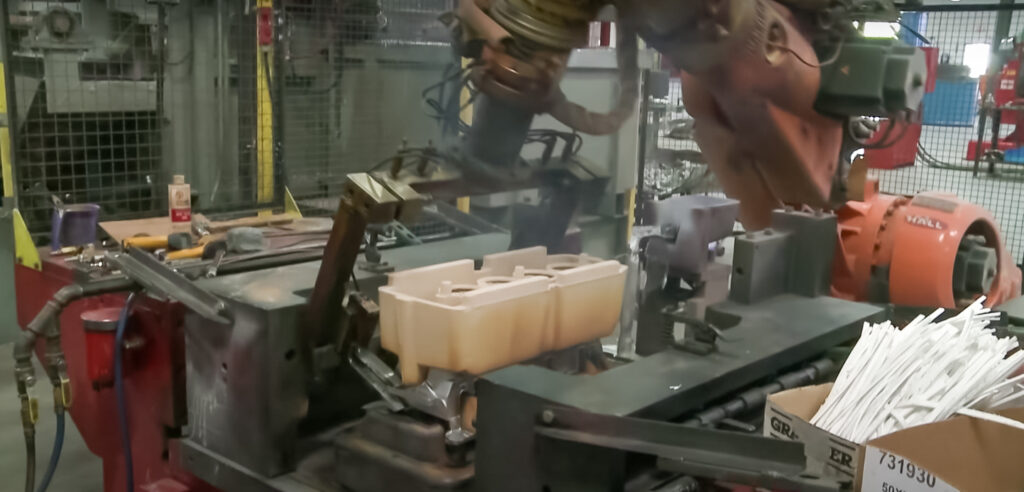
Robotic ladling systems introduce liquid aluminum to the castings. Three ABB and one Kuka 100-pound bottom-pour ladling robots pour aluminum at a preset value for unmatched consistency. The unique bottom-pour design fills the ladle below the metal surface, resulting in reduced dross and turbulence for a more consistent casting quality.
As stated, dry sand is for short runs, as only a few pieces can be cast from one dry sand tooling. However, dry sand is virtually free form; they are not restricted in size as much and can do a large mold of 3×4 feet. “For example, the Edelbrock Jeep head is cast from dry sand due to its length,” Emerson says. “We make about 300 per year, which would be considered a high volume on dry sand. The largest part cast in dry sand consistently is the big race cylinder heads for the Edelbrock/Musi 555. Those things are massive.”
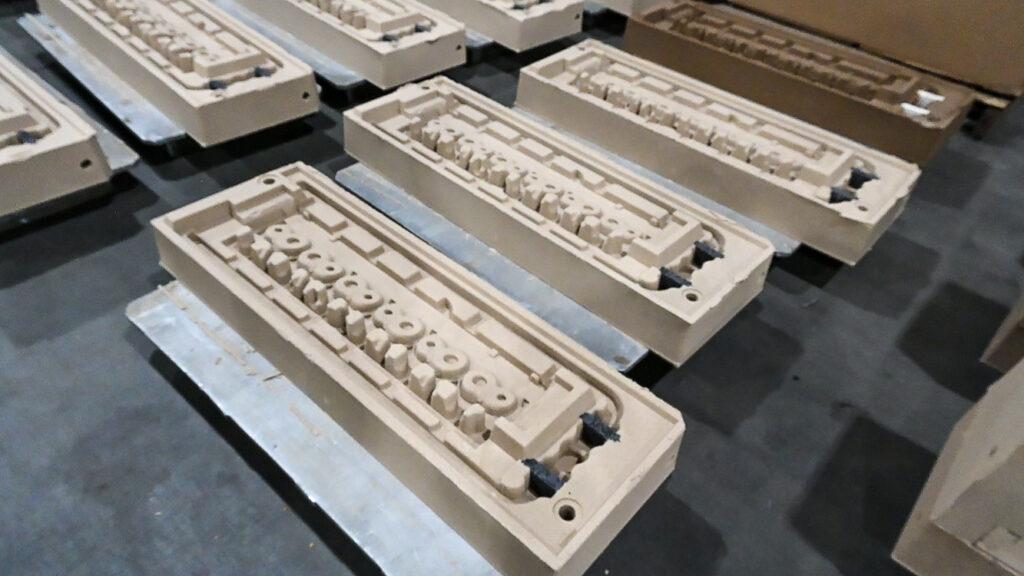
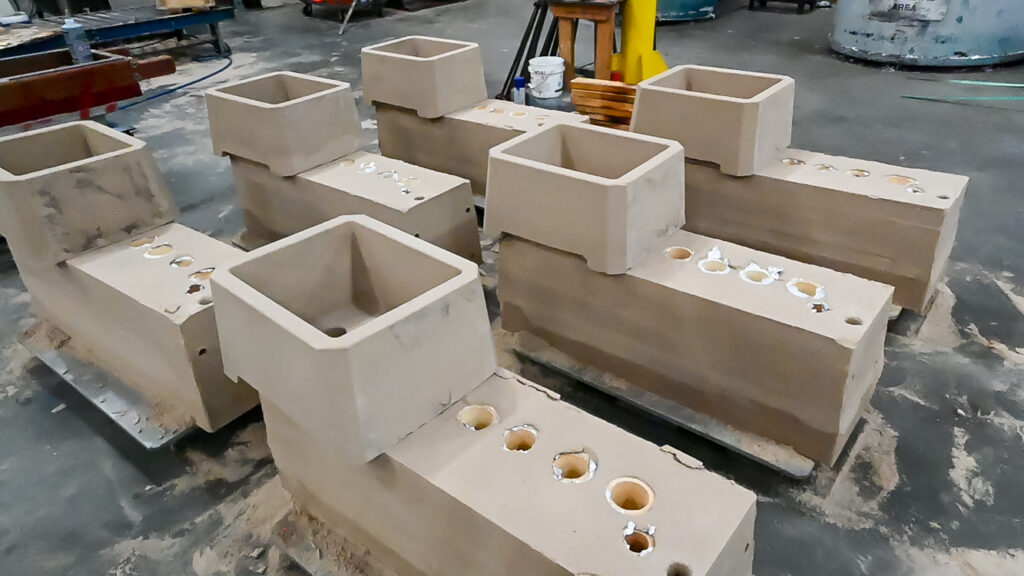
Green sand casting is performed on three automated mold lines capable of complex, core-intensive castings of up to 60 pounds. Two fully automated cope-and-drag molding lines supported by a high-volume green sand handling system can produce a part up to 20×30 inches. The third line is a Sinto match-plate flask-less molding machine capable of producing a part 20×24 inches.
“We are much more efficient on our green sand lines,” Emerson explains. “Each line runs between 40 to 60 molds per hour, so we are pumping out about 200 castings per hour total. The biggest thing we have run on those lines was the Hellcat supercharger case. We made about 120,000 of them.”
The largest volume of parts the Foundry runs per year are intake manifolds to the tune of approximately 100,000 per year. Second to that would be cylinder heads (both Edelbrock and private-label), with about 50-to-60,000 made annually.
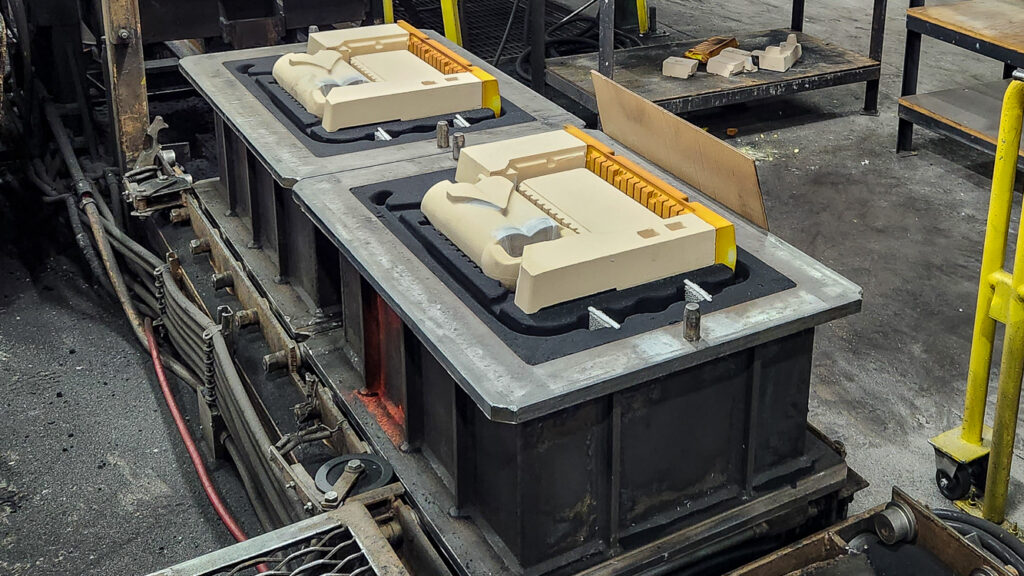
Core Removal and Cleanup
The final step of production is the removal of the cores from the casting. Cores are removed using automated Hershal or A-frame vibratory machines. Once separated from the cores, the new castings are sent to clean up, where the gating and burrs are removed either by hand, high-tech robotics, or the previously mentioned deburring machine. The result is a high-quality machine-ready casting. The Foundry is also capable of machining the part into a finished product.
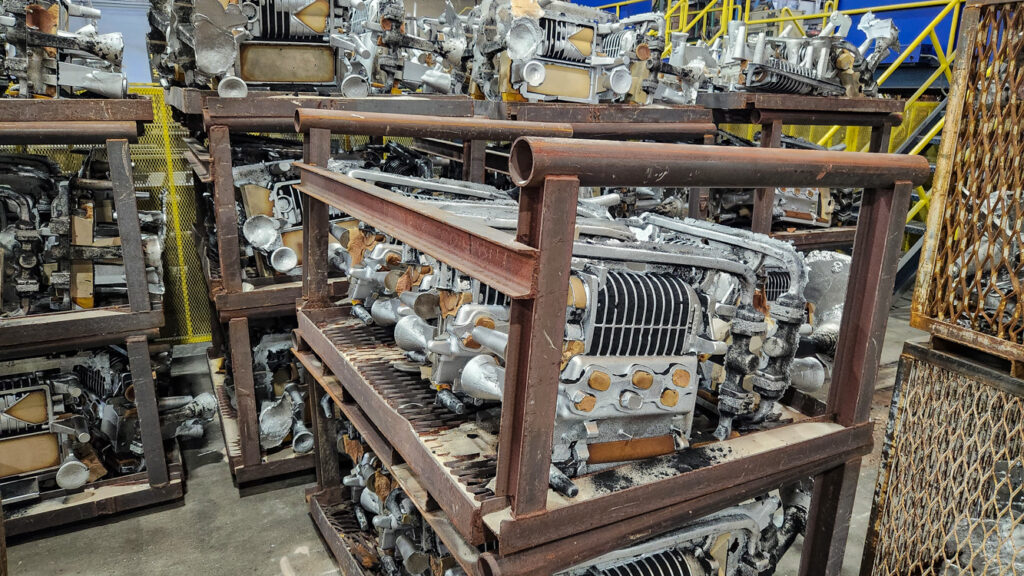
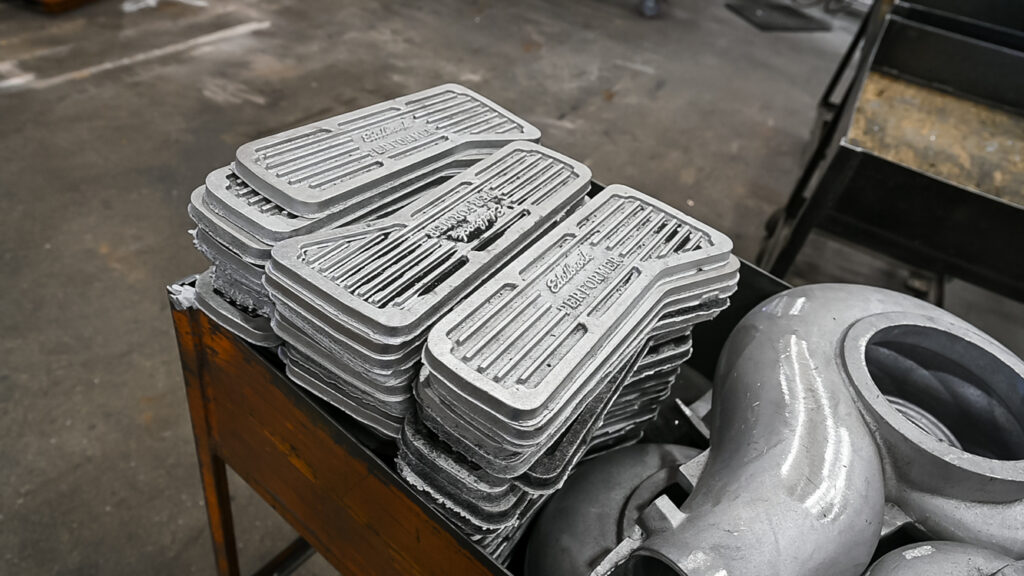
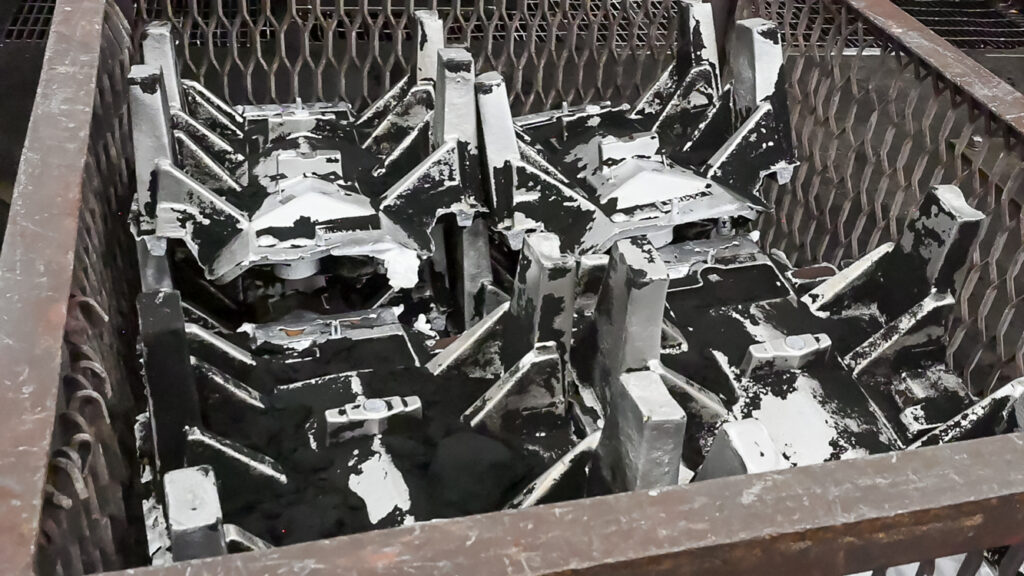

In the Market?
The Edelbrock Foundry is growing and ready to take on more clients. So, who is the perfect client? Beyond saying anyone with a need for aluminum castings, there is a sweet spot for production versus cost. The Foundry is set up as a medium-to-large job shop, but they are not looking to run millions of castings for one client as it would take up too much production time.
“Every line changes over three to four times per shift,” Morse says. “We are not looking for OEM-size production like half-a-million water pumps for Chevrolet or anything like that. Depending on the complexity of the part, our sweet spot is anywhere from 1,000 to 60,000 units annually, depending on the type of mold. Beyond that, it can put a strain on our production cycles, so 200,000 is out of range.”
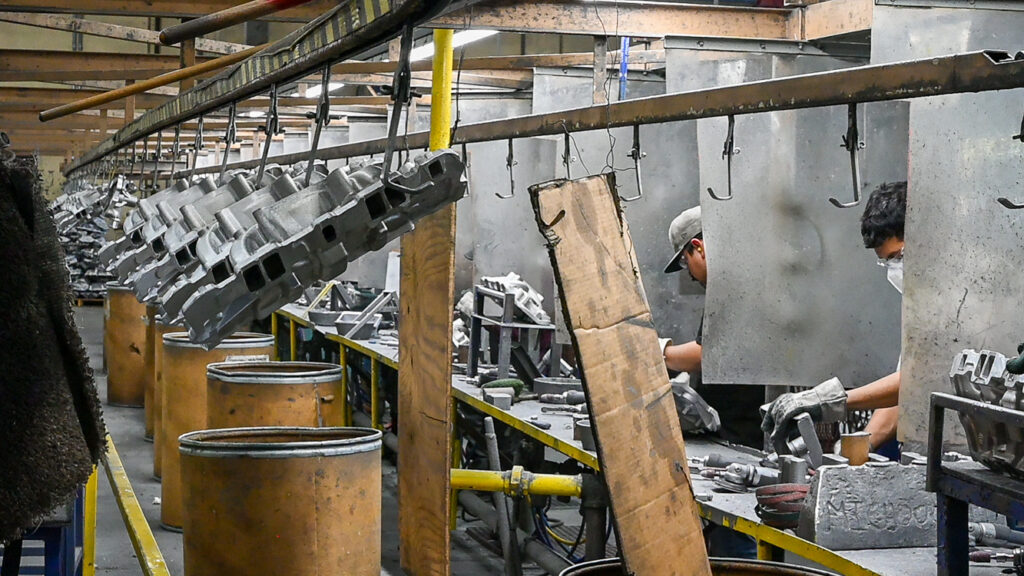
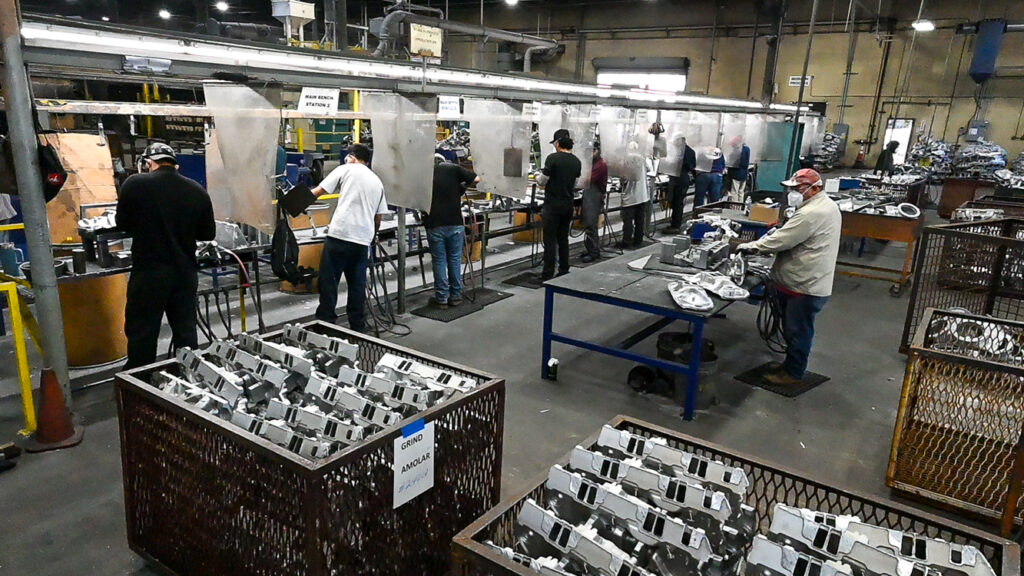
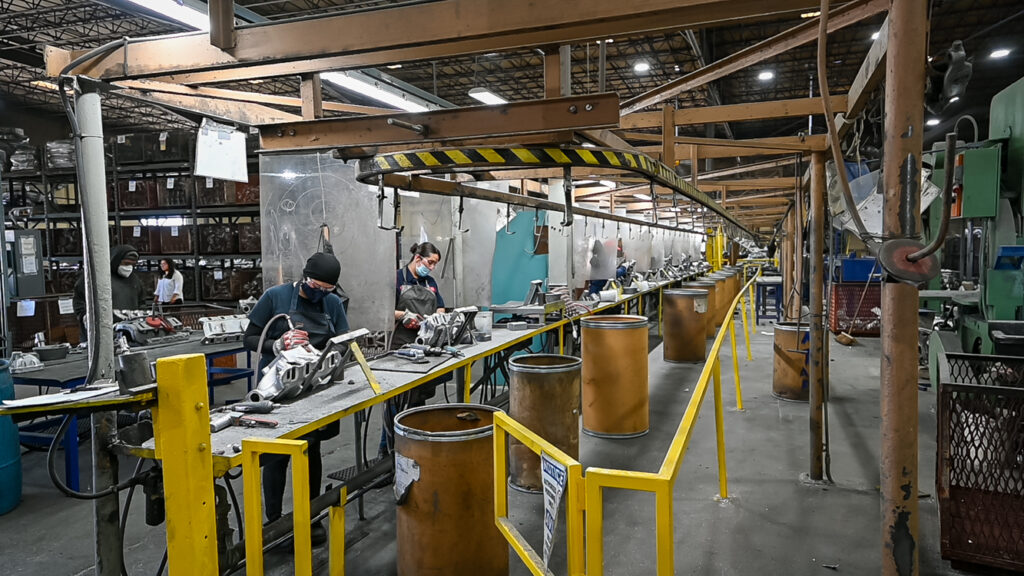
The EV market is one area where Morse sees an opportunity for the Edelbrock Foundry. There are many aluminum parts for EVs that could benefit from the Foundry’s abilities with rapid prototyping as things are changing so rapidly with the new technology. Obviously, EVs are still in the automotive realm. But from Emerson and Morse’s perspective, EVs represent a diversification from the normal aftermarket parts they are known to run; to them, it might as well be a different industry.
Emerson notes their ability to provide turnkey cast-machine parts as a significant step in the right direction for clients’ needs. “One of my points of focus is to be able to provide that turnkey product,” he says. “From people I have spoken with, that is what they want now. They do not want to go through all the steps to assemble everything. The more they can consolidate under one roof, the more opportunities it will open for us.”
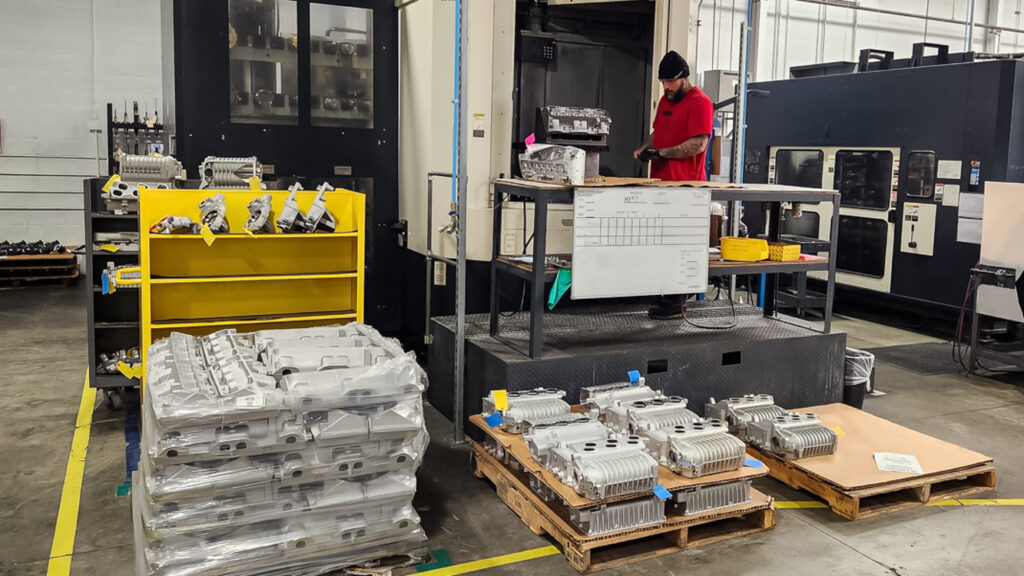
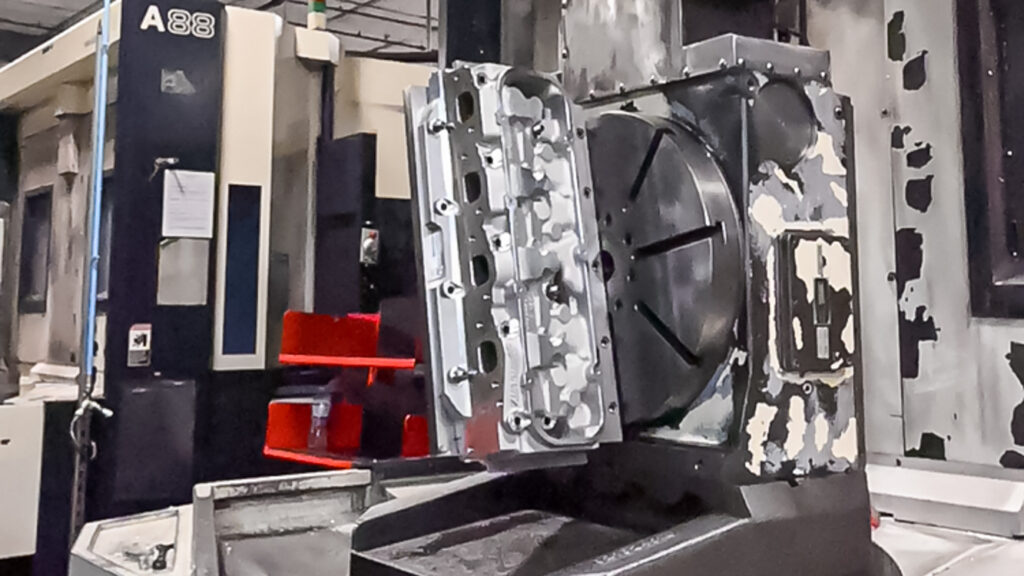
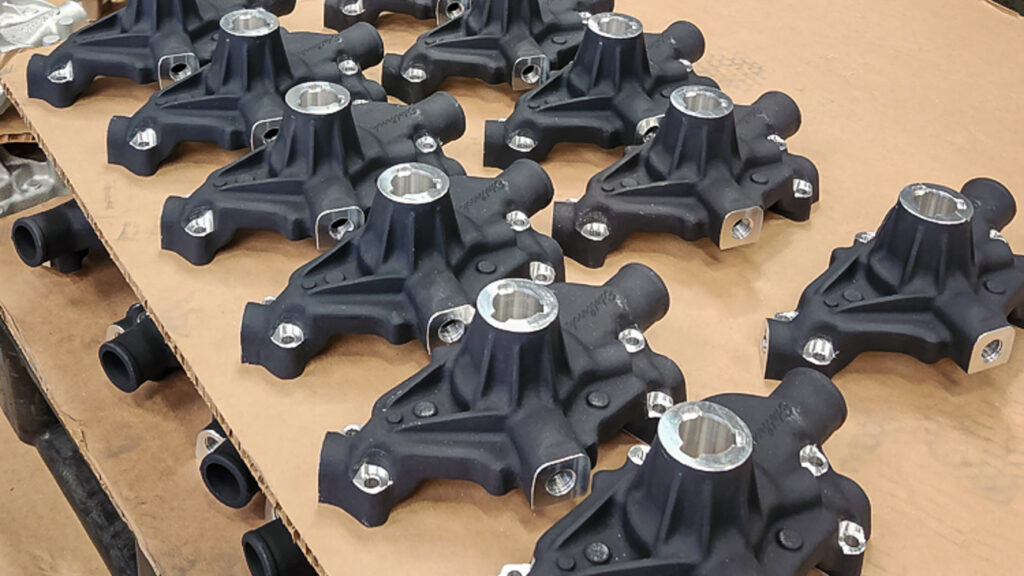
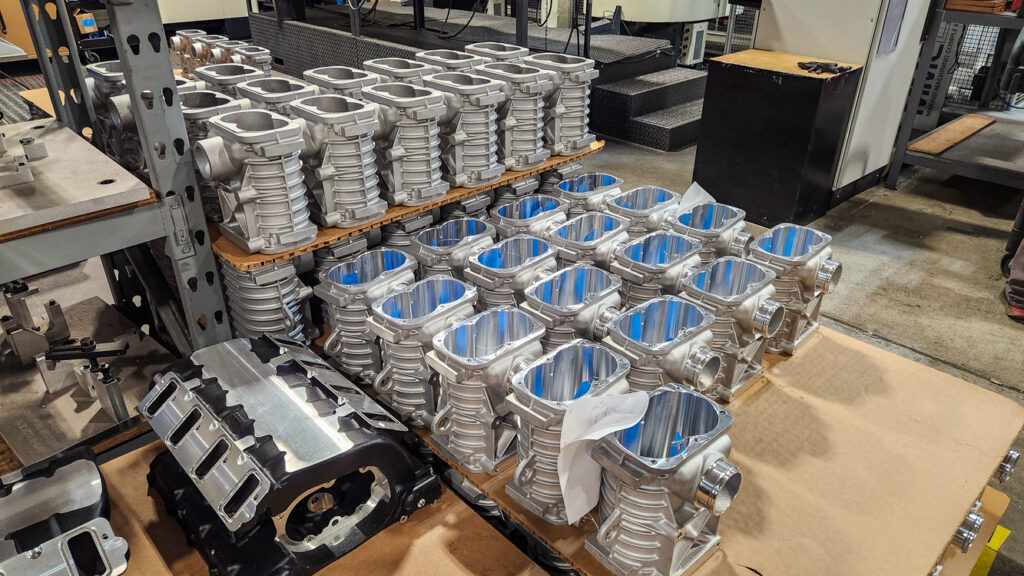
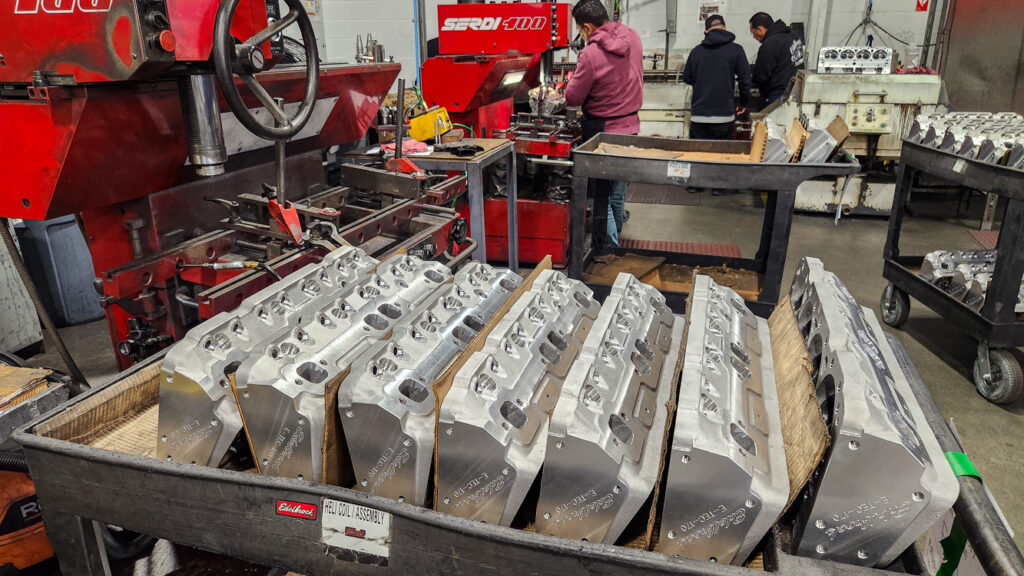
Conclusion
The Edelbrock Foundry website has a landing page where a potential client can conveniently inquire about its services and get a quote. Just fill out the form with some basic information, and someone on Morse’s team will contact you for more information. Looking at the list of clients on the website, you can understand the quality you can expect.
The Edelbrock Foundry is truly a world-class facility that is growing and diversifying into realms that Edelbrock Jr. would never have imagined when he opened the plant in 1990, and it’s for the better. You can count on the Foundry for the same high-quality made-in-the-USA aluminum parts for which Edelbrock is known. If you are in need of aluminum casting, contact the Foundry and see what they can do for you.
Foundry Videos
If you are a “how-it’s-made” type of person, here are a few YouTube videos showing the core manufacturing processes that will certainly pique your interest.