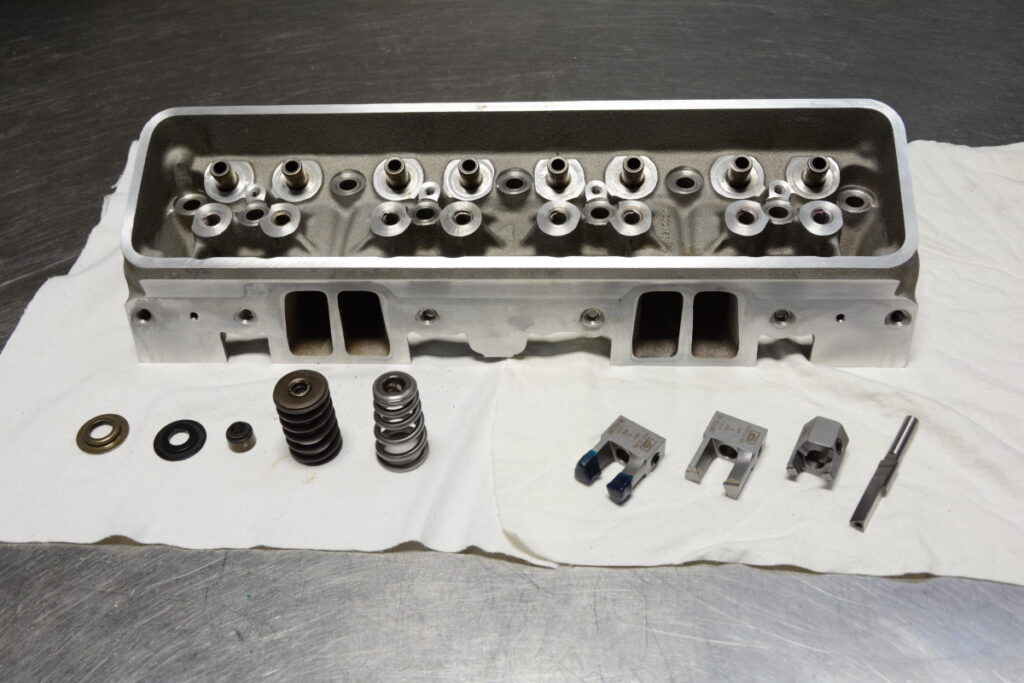
Modifying heads to accommodate higher valve lift can seem like a daunting task. However, with a little knowledge and the right tools, it can be done by most people who know their way around a tool box.
Our LT1 project includes a higher lift cam and a set of new COMP Cams conical valve springs designed for an LS. Our LT1 heads are aluminum, but the procedure should work on cast iron heads, as well. Wanting to keep the budget low, we decided to skip the machine shop and do it ourselves using hand tools.
Stock lift capabilities on our heads topped out around .525”, but we want more…MORE! Say in the neighborhood of .600. Simply adding a taller cam lobe would cause the spring retainer to bottom out on the valve seal; the valve guide is simply too tall. Additionally, it’s also too wide in diameter for the spring package we wish to run. We need to shorten the valve guide and trim the outer diameter down for the new seals.
Our first step was to use a seat cutter to straighten up the spring seats. The stock spring bases measured 1.25”. Our new spring seats were a little bigger at 1.340, but we had plenty of room around the base. Some cast iron heads have sunken seats and may require a little more attention.
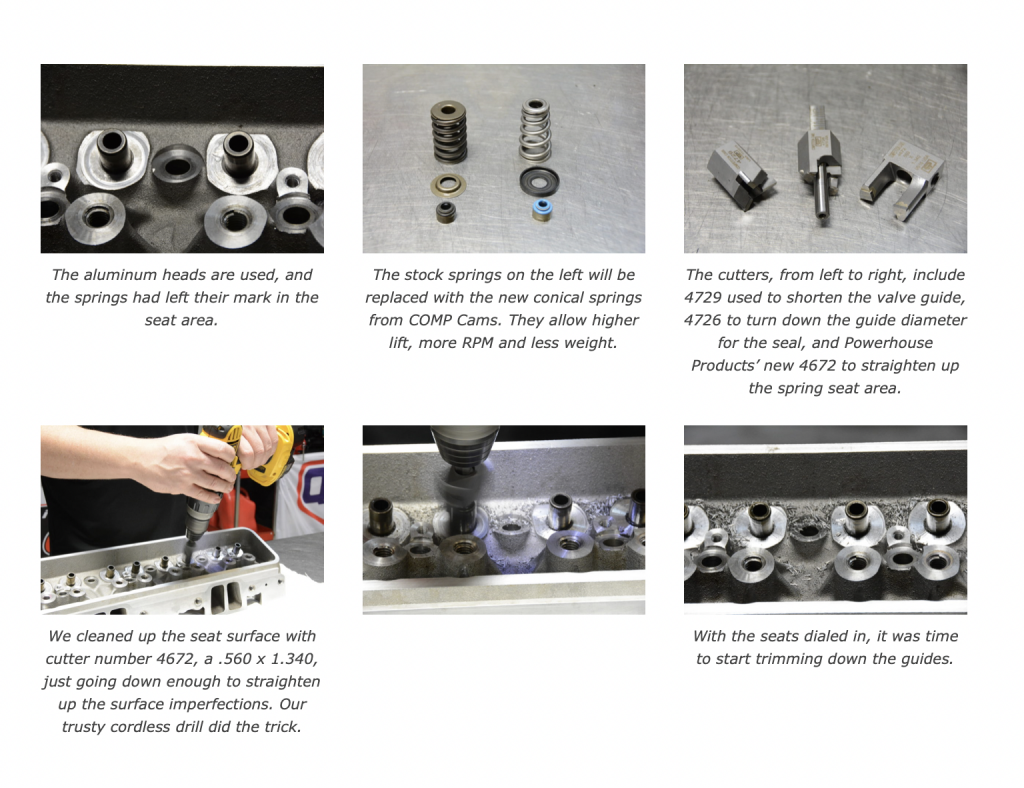
As the photo shows, several of our seats were pretty banged up on these used heads. We used Powerhouse Products‘ new seat cutter (.560 x 1.340 — Part No. 4672) to plane the seat down smooth and level. From that starting point, we broke out the micrometer to measure the guide, which checked in at .715.
With our .600 valve lift, spring retainers and installed height, we determined we’d like to shave the guide down a hundredth or so. We trimmed a piece of aluminum down to .600 to act as a stopper for the cutter tool. In a machine shop, the drill press would come down the proper amount, but we were using our trusty cordless drill. With the softer aluminum piece, the cutter tool just starts spinning when we hit it at our proper depth. A stopper could also be made with any combination of flat washers, nuts, etc. if aluminum wasn’t available.
We used cutter number 4729 to trim the guide down. This tool is usually used to cut rocker arm stud bosses down to convert from press-in rocker studs to threaded. We swapped out the larger arbor and pilot (Part No. 4732) with the one we used in trimming the seat base down, as it was the right diameter to fit inside the valve guide. With the cutter chucked into our cordless, and a few drops of cutting oil, we applied light pressure and let the bit cut through the guide until it bottomed out on the aluminum stopper.
With the guides trimmed down to the proper height, (and it worked beautifully) we then switched over to the seal step cutter. Our seals measure .365 in height, and our cutter goes down to .385, leaving plenty of room. The inner diameter of the new seals measured .530, so they needed to be turned down .030 from the stock diameter of .560.
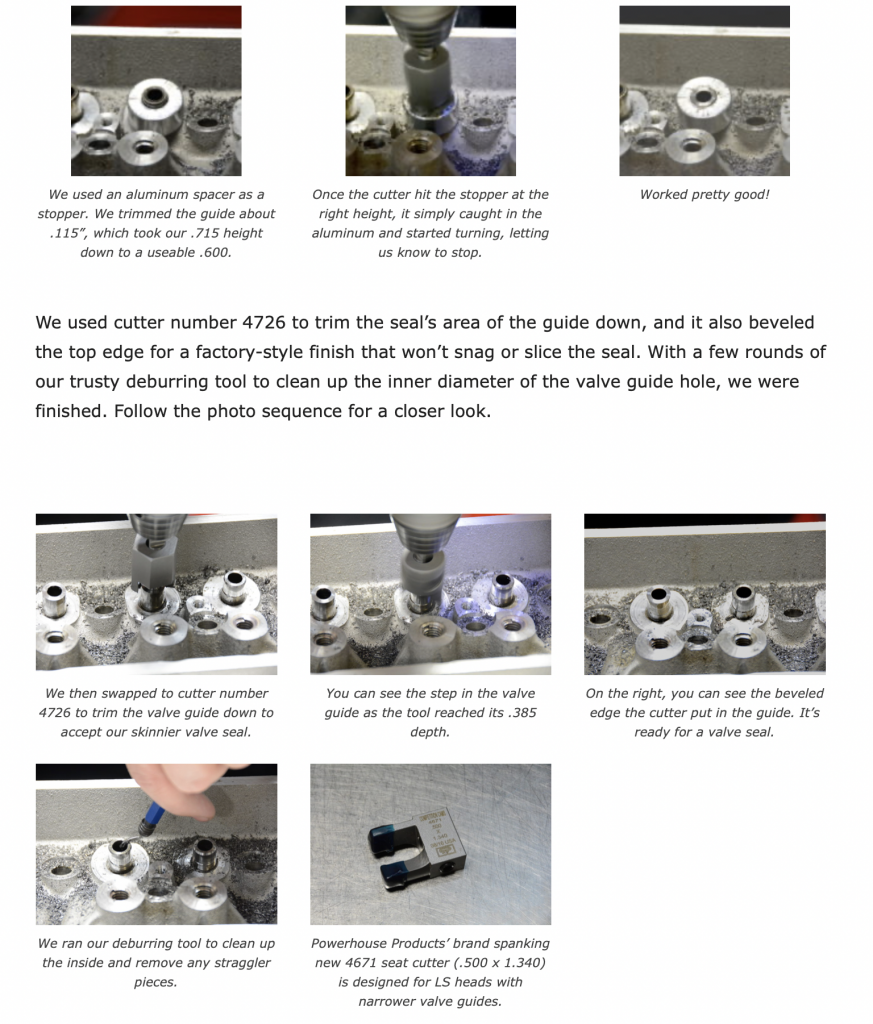
We used cutter number 4726 to trim the seal’s area of the guide down, and it also beveled the top edge for a factory-style finish that won’t snag or slice the seal. With a few rounds of our trusty deburring tool to clean up the inner diameter of the valve guide hole, we were finished. Follow the photo sequence for a closer look.